Get custom cabinets on a budget by making them yourself! Learn how to build a simple base cabinet box with quick and easy frameless construction.
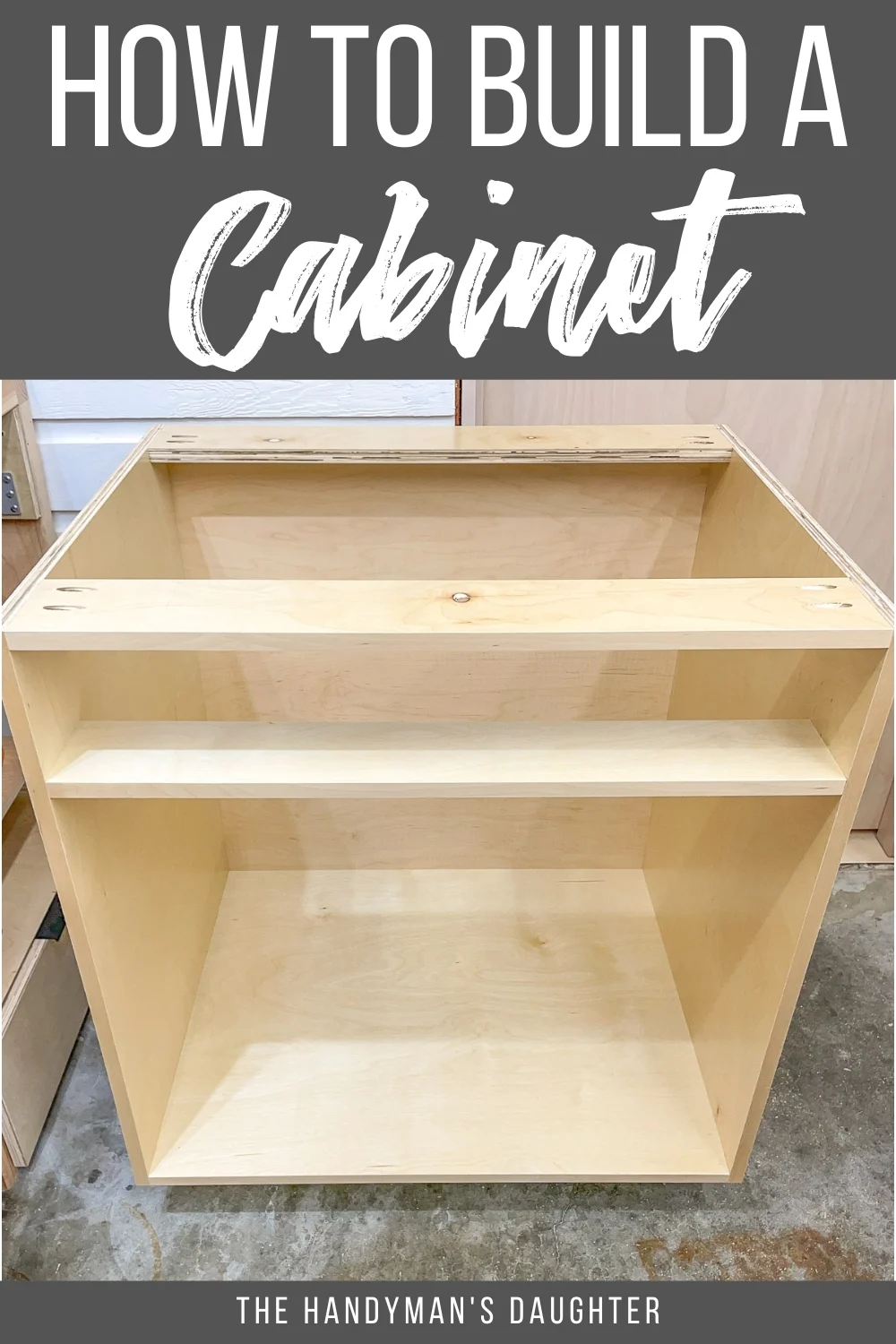
Building cabinets sounds like a big, scary project, but it's really just a bunch of boxes! In this cabinetry series, I'll first show you how to build a simple cabinet box. In later tutorials, I'll go over how to add drawers, pull out shelves and hidden trash can compartments to customize your base cabinets.
I'm building these cabinets as part of my long-awaited kitchen remodel! I've painted the cabinets and backsplash, and covered the countertops with contact paper to make it less terrible, but it's time to rip off the bandaid and start from scratch!
I'll be working on this huge project in sections, starting with this random grouping of cabinets. It will be transformed into a symmetrical bank of upper and base cabinets with a long countertop spanning the entire wall.
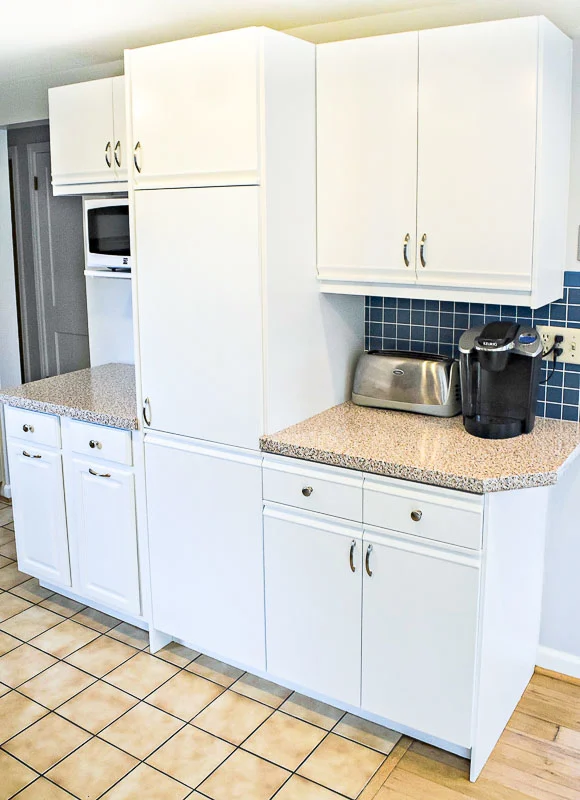
Once the base cabinets are installed, I started building the DIY wall cabinets. I'm hoping that by working in sections like this, I'll minimize the disruption in the kitchen and I won't run out of room in my workshop!
Don't forget about the doors! Check out this article about the different types of cabinet doors to learn more about the various styles to choose from. Once you've decided on a style, download my free worksheet to help measure for cabinet doors correctly! Then check out my tutorial on how to build Shaker cabinet doors yourself!
[convertkit form=3262547]This post contains affiliate links for your convenience. Purchases made through these links may earn me a small commission at no additional cost to you. Please visit my disclosures page for more information.
Things to Consider
Before you start cutting and assembling, there are a few things you should consider. By planning ahead, you can prevent a lot of errors and build a better cabinet box!
Choose your plywood wisely
There are a lot of choices when it comes to the different types of plywood, but not all of them are great for building cabinets. Typically, you want to look for sheets that are labeled "cabinet grade" for better quality. If you're putting in all this effort, spend a few extra bucks to ensure that they last and look good!
There's usually a "good" side to the plywood sheet. This side should be free from knots and imperfections. The other side will be of a lesser quality, but will likely be hidden, either by the wall, an adjoining cabinet or an end panel. Use the good side for the interior of the cabinet.
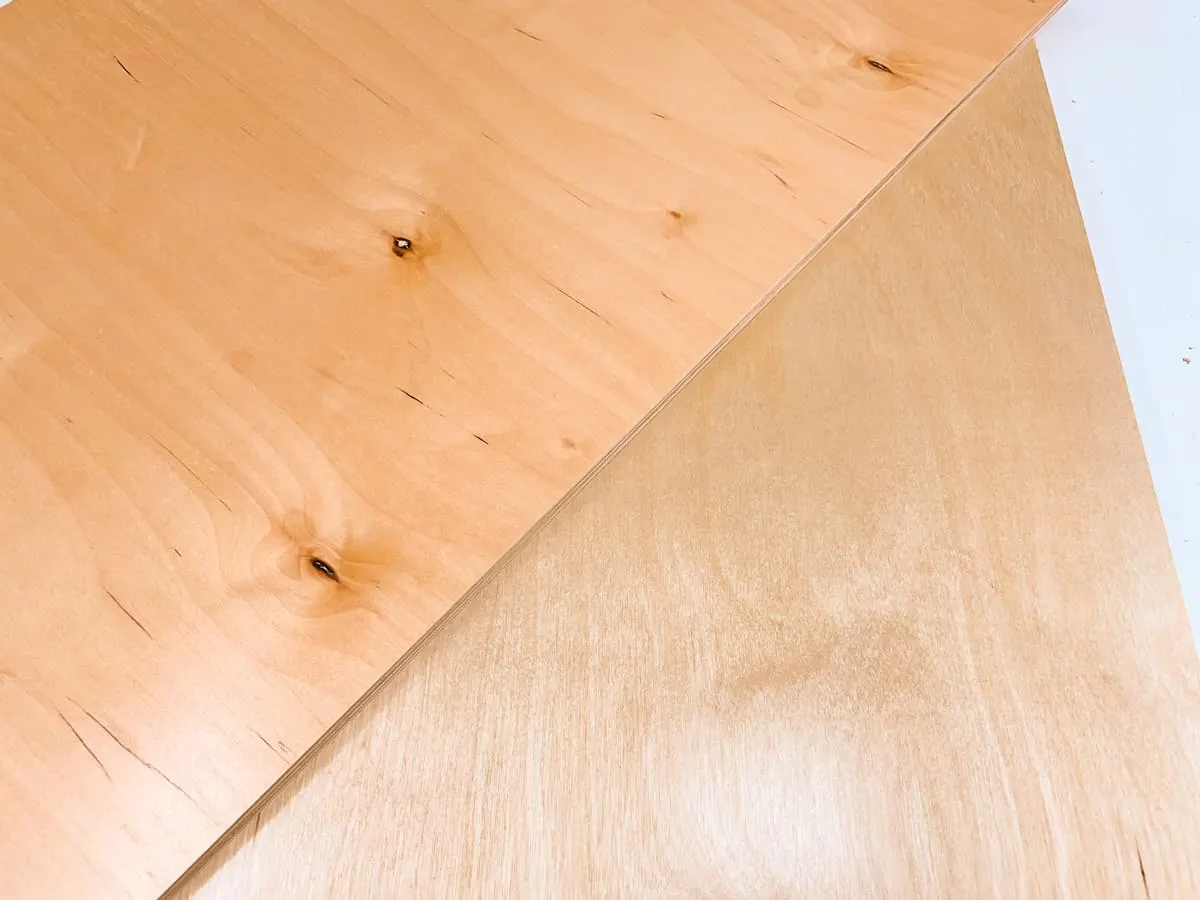
My cabinets are made from prefinished birch plywood (that's why it's shiny). Prefinished means that a clear protective top coat was applied at the factory, saving me a ton of time! I plan to paint the doors, drawer fronts and end panels, but the inside of the cabinet will remain natural wood with a clear coat.
Plan your plywood cuts
One of the hardest parts about working with plywood is that the sheets are so big! I have ¾" plywood sheets cut down the middle lengthwise at the store. This gives me two 2'x8' panels that fit into my car and onto my workbench easily.
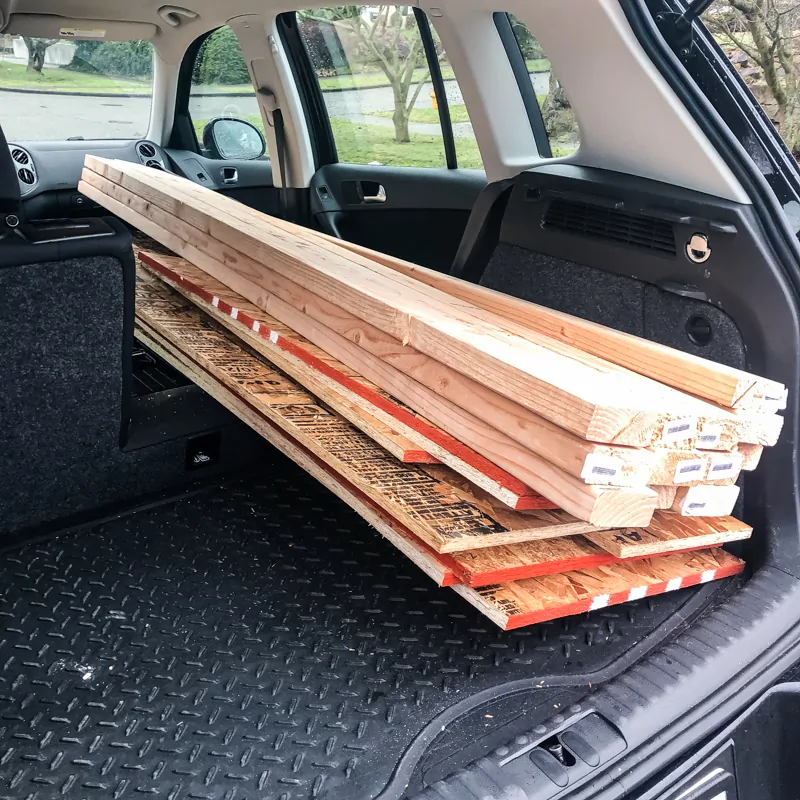
Pay attention to the wood grain direction when planning your plywood cuts. The grain should run vertically up and down the side pieces, and across the width horizontally on the bottom and shelves. If you have the plywood precut to these long strips, the grain direction is already correct!
Draw out a rough cut diagram to get the best use of your material without a lot of waste. I usually plot out the bigger pieces like the sides and bottom first, then use scraps for the stretchers and nailer strips. I explain the different parts of a cabinet in this article if you're not familiar with these terms.
Separate toe kick or integrated toe kick?
The cabinet toe kick is the part at the bottom that raises the box up off the floor. It's set back 3-4" from the front of the cabinet and 3-4" from the bottom. This gives you room for your feet while you work at the counter, so you're not leaning over constantly.
There are two ways to create the cabinet toe kick. You can build a separate platform for the cabinet to rest on, or you can integrate it into the side pieces and cut out a notch at the bottom.
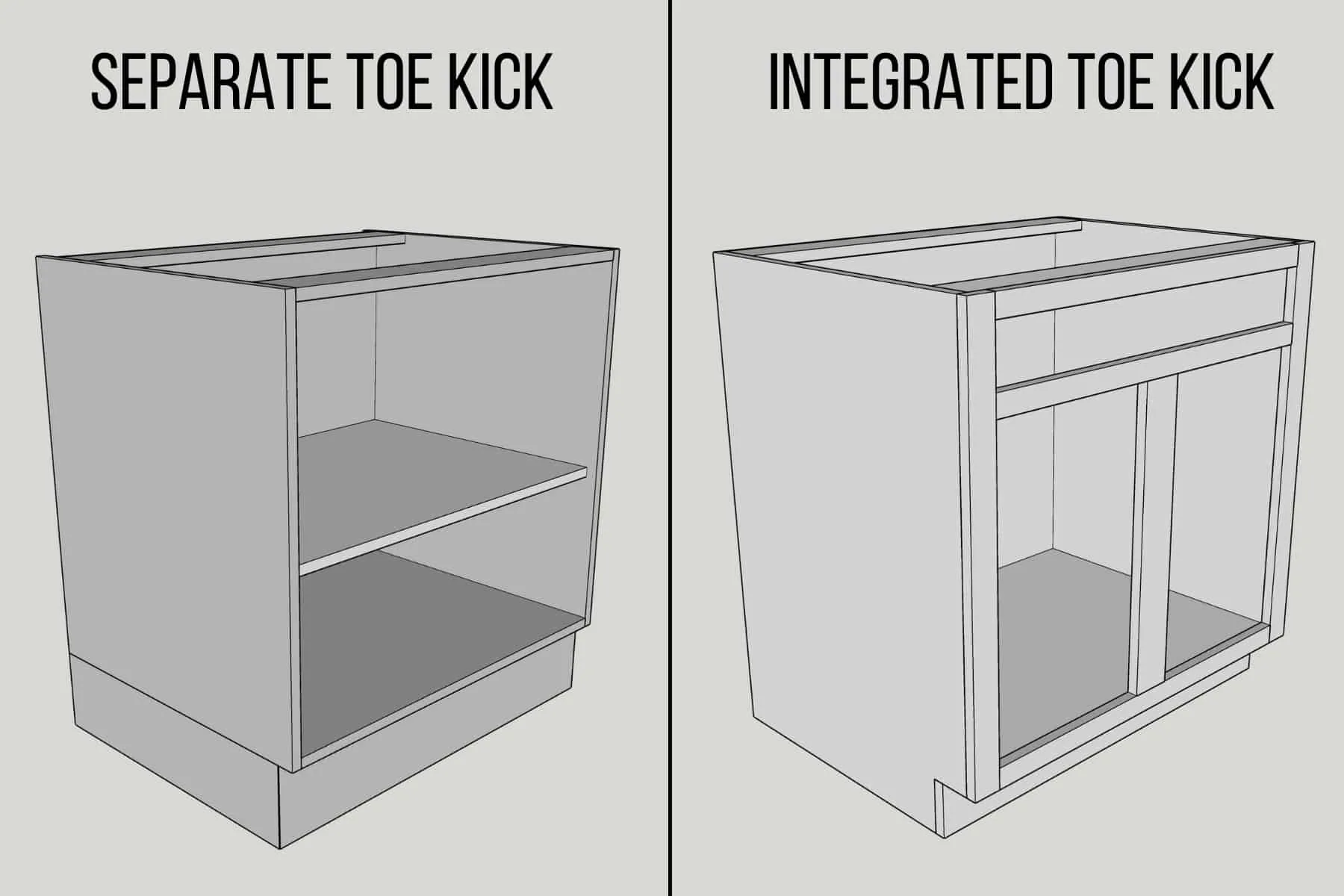
I'm building a separate toe kick platform instead of integrating it into the side pieces. This saves on materials, since I'm able to get almost all the pieces for two base cabinets out of a single sheet of plywood! Plus, it's easier to level a small platform rather than a huge cabinet when it's time for installation.
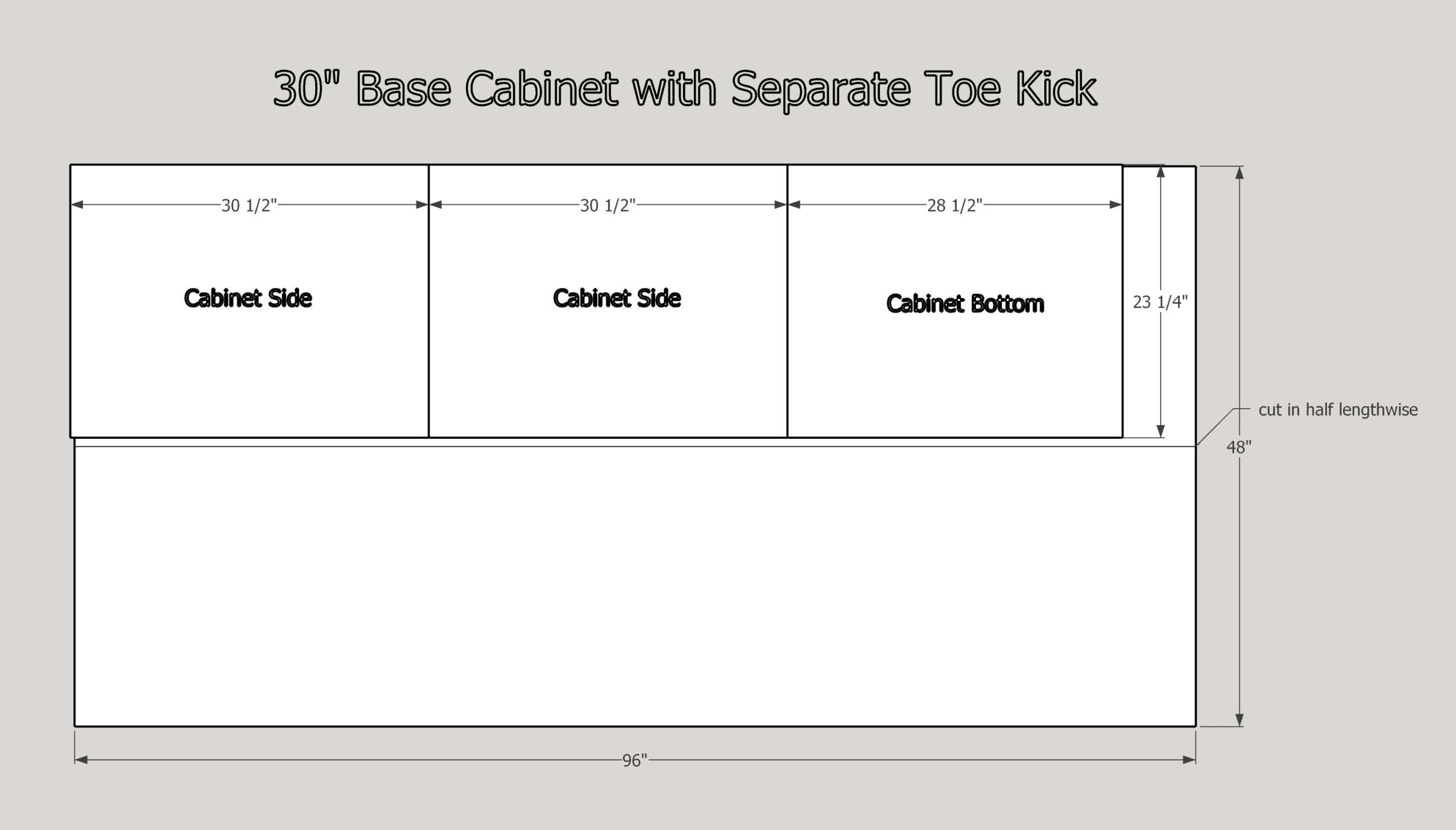
Add 4" to the height of the side pieces for integrated toe kicks. If you're making a standard 30" wide base cabinet, you'll need to use the other half of the sheet for the bottom.
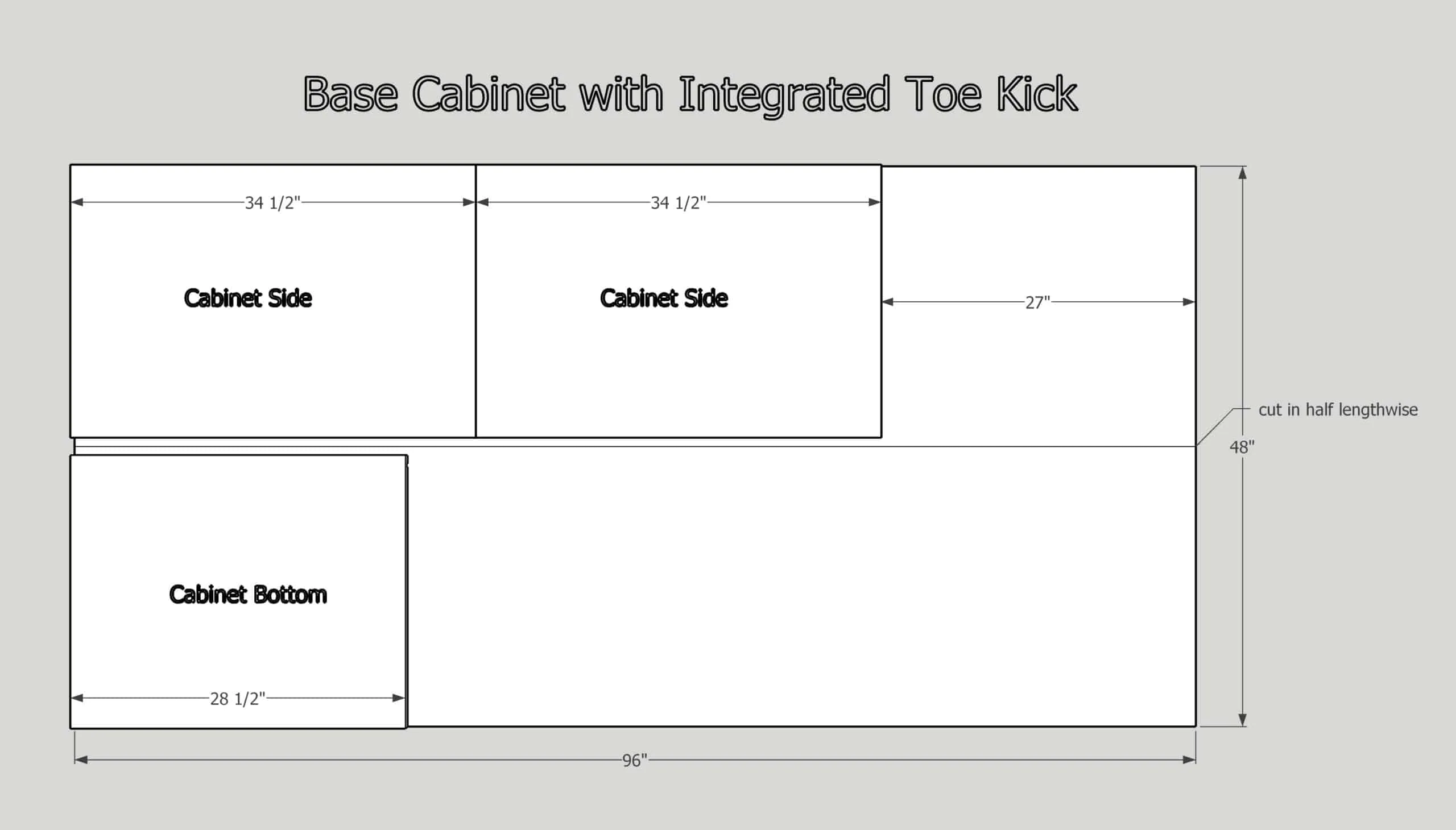
Label your pieces
Cabinet box pieces all start to look the same, especially if you're making a bunch of them at once. Instead of driving yourself crazy trying to figure out which piece goes where, label them as you cut them out!
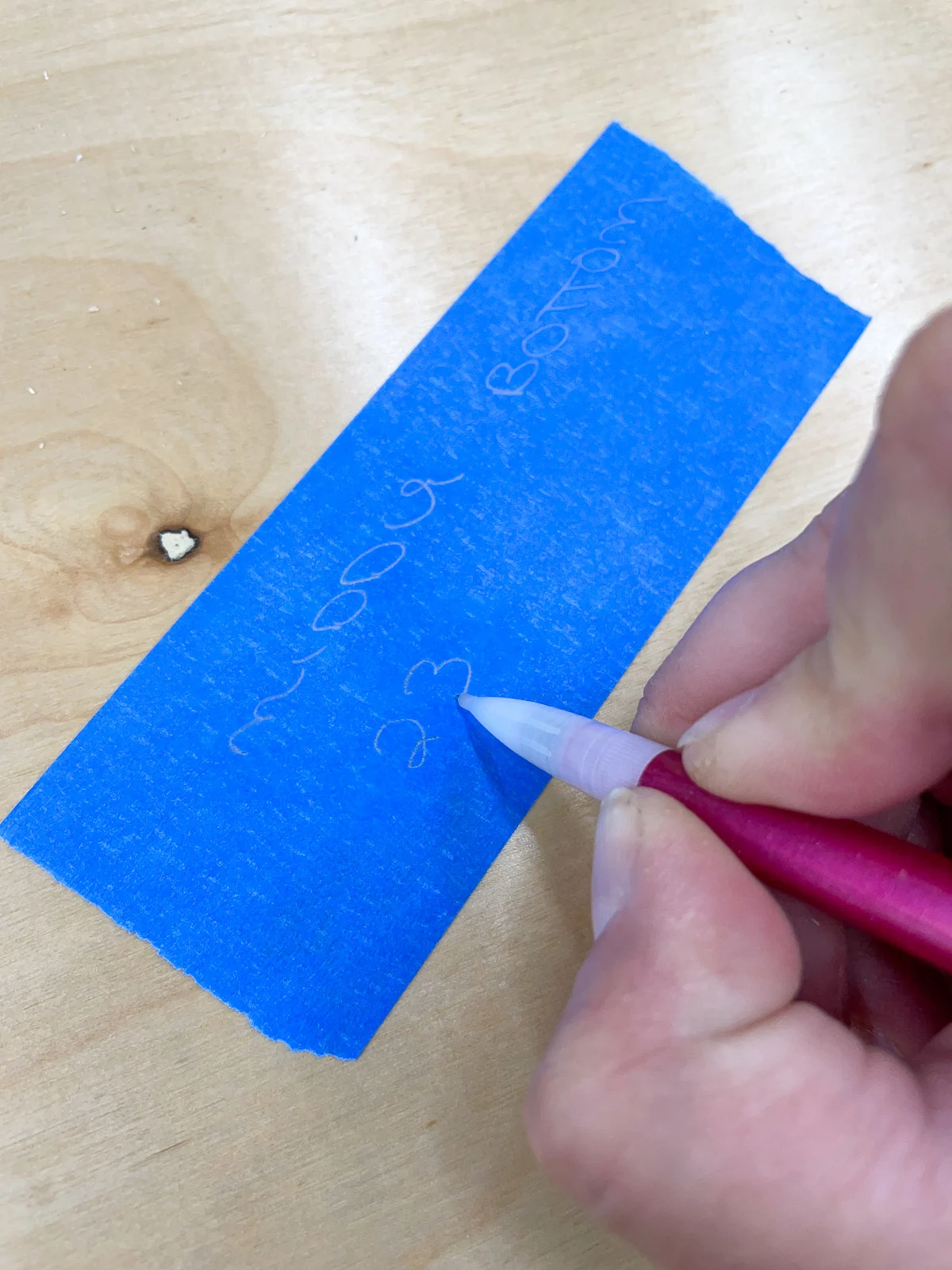
I stick a piece of blue painter's tape to every piece with the part name and dimensions written on it. Even if all the pieces are in a giant stack on the workbench, I know which part goes where so I don't accidentally use a side piece as the bottom!
How to Build a Base Cabinet
Cut the plywood pieces to size
Even though the 2'x8' sheets are a little easier to handle, they're still too big to push through the table saw safely. I prefer to use a track saw to break down the larger sheets into the rough size needed for each cabinet part.
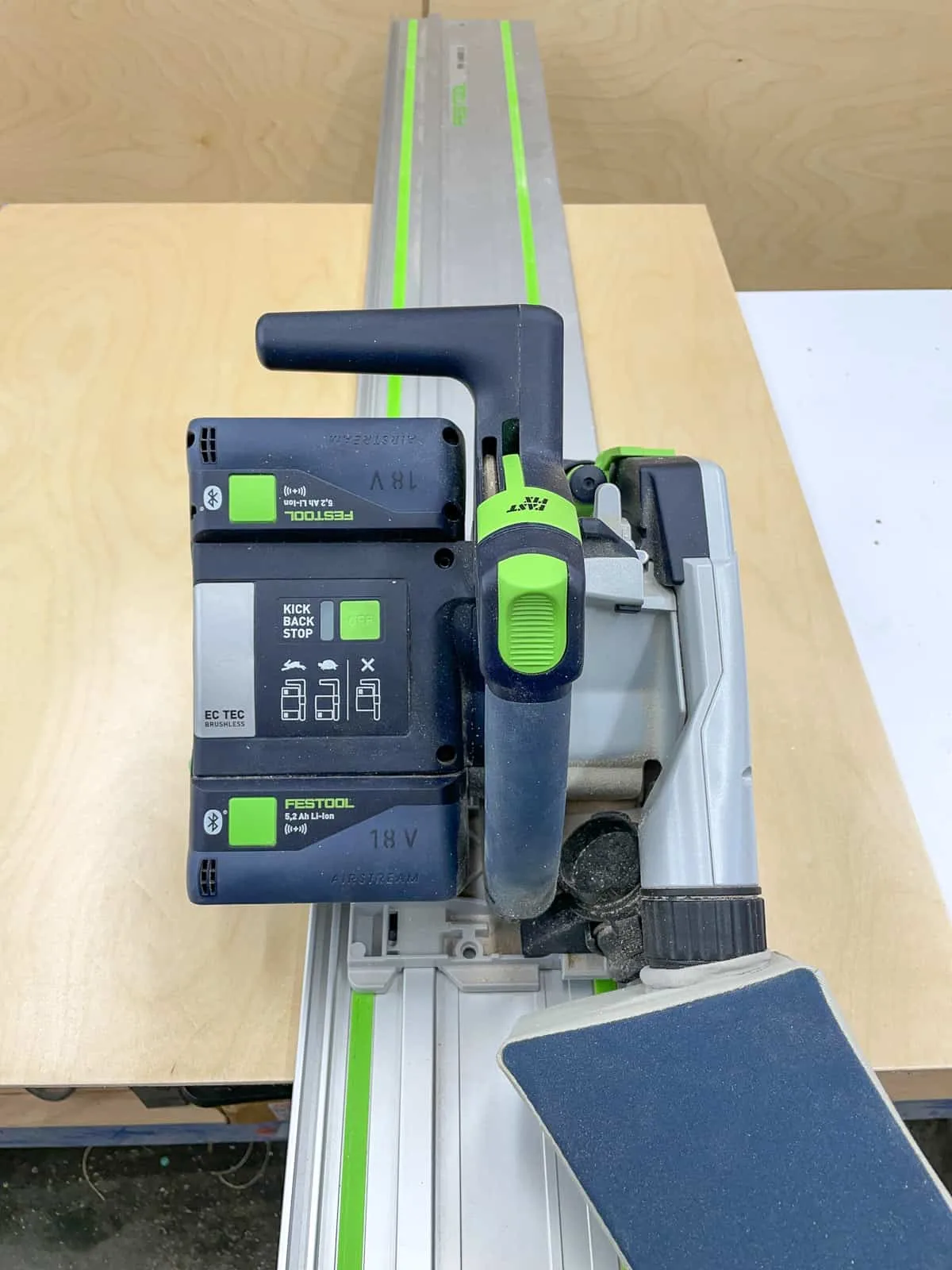
You could also use a circular saw, although you'll need to use a circular saw straight edge jig to keep your cuts straight. I have an entire article comparing a track saw vs a circular saw if you're interested in learning more about these two tools.
One benefit of the track saw is that it can make really clean cuts, but I still like to use blue painter's tape to prevent tear out on the cross grain. Make sure to check for square before you cut, and use the factory edge as your reference edge.
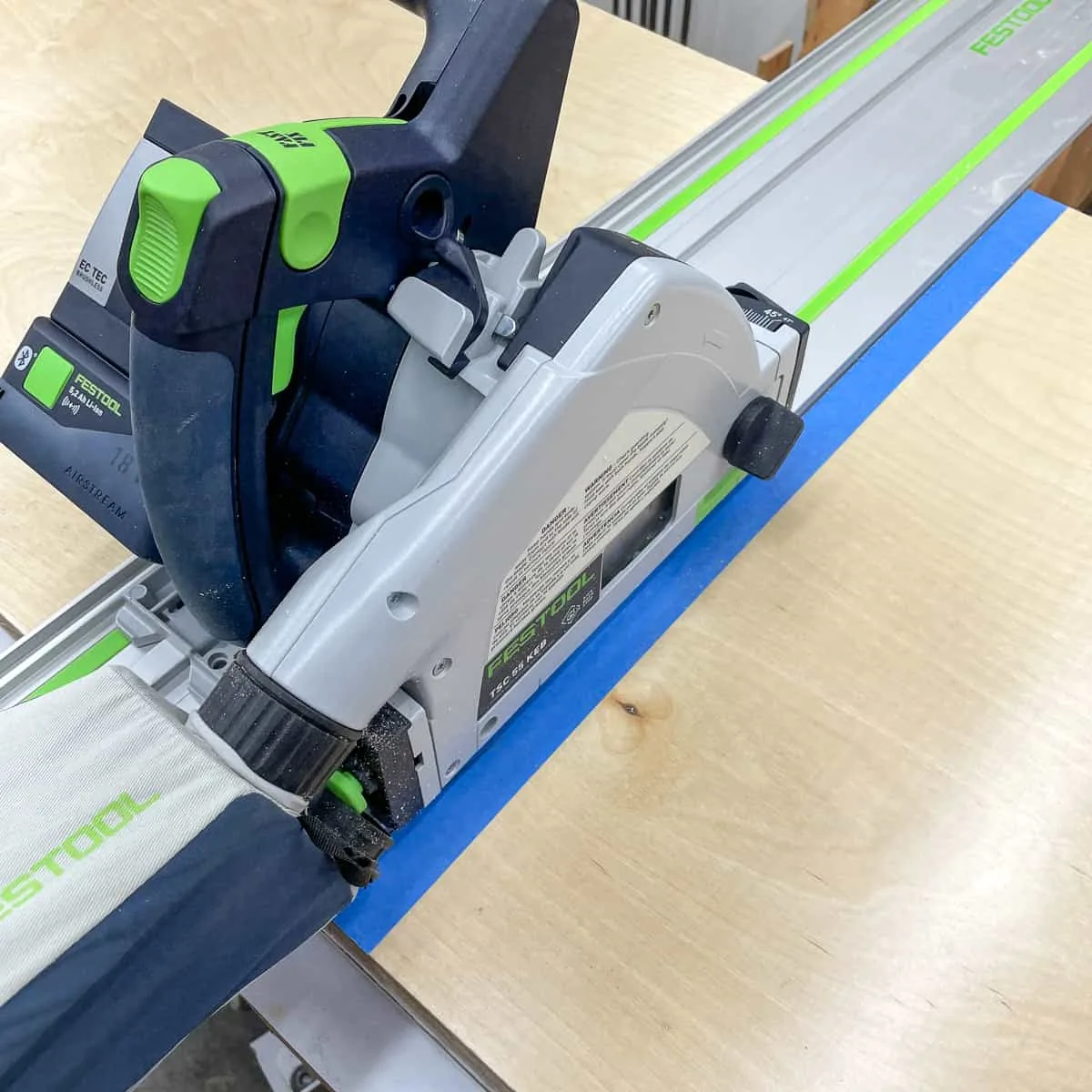
Once each cabinet piece is cut to the correct height with the track saw, it can finally fit on the table saw! Trim off the rough, splintered edge that the store's saw made down the middle first, using the factory edge against the fence.
For the last cut, move the fence to the final width to remove the factory edge. Use this fence setting for all the side and bottom pieces, so they'll be exactly the same size.
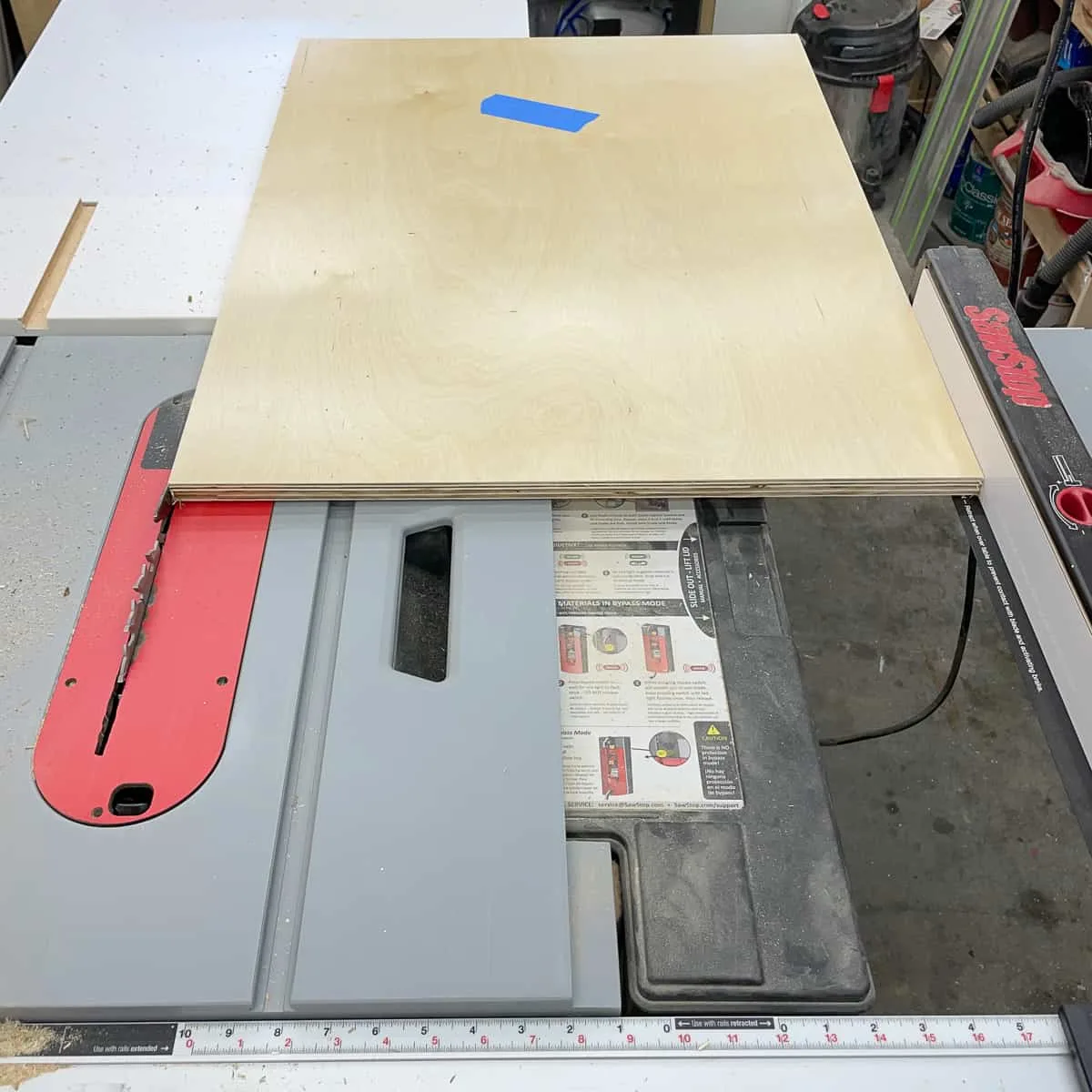
Use leftover ¾" plywood to cut 4" wide strips for the front and back stretchers. I usually dig around in my scrap lumber cart for the nailer strip pieces, since they'll be hidden behind the back of the cabinet.
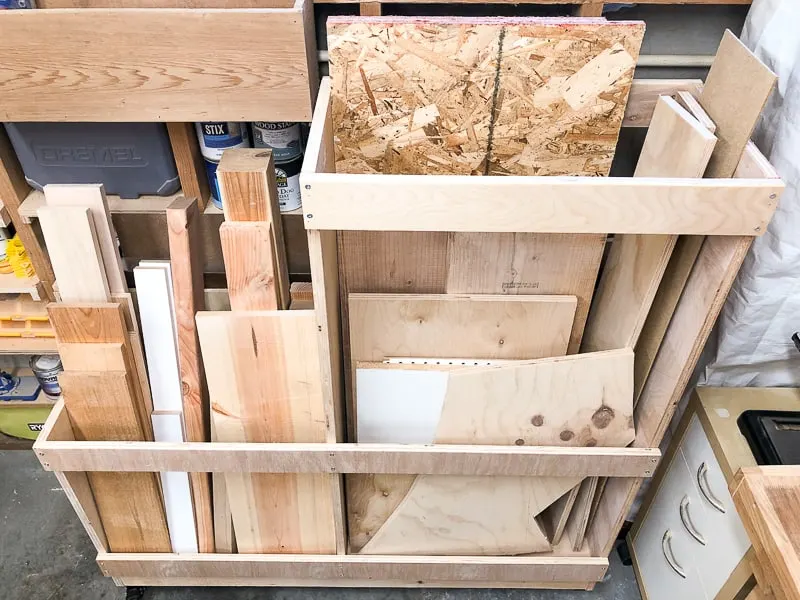
Finally, cut the back panel out of ¼" plywood. It should be ¾" less than the height and width of the finished cabinet box. It will be recessed into the grooves that will be cut in the next step.
Cut the grooves for the back panel
There are a few different ways to attach a cabinet back panel. I prefer to cut a groove for the panel to slide into. It's quick and easy to do at the table saw, and it hides the nailer strips.
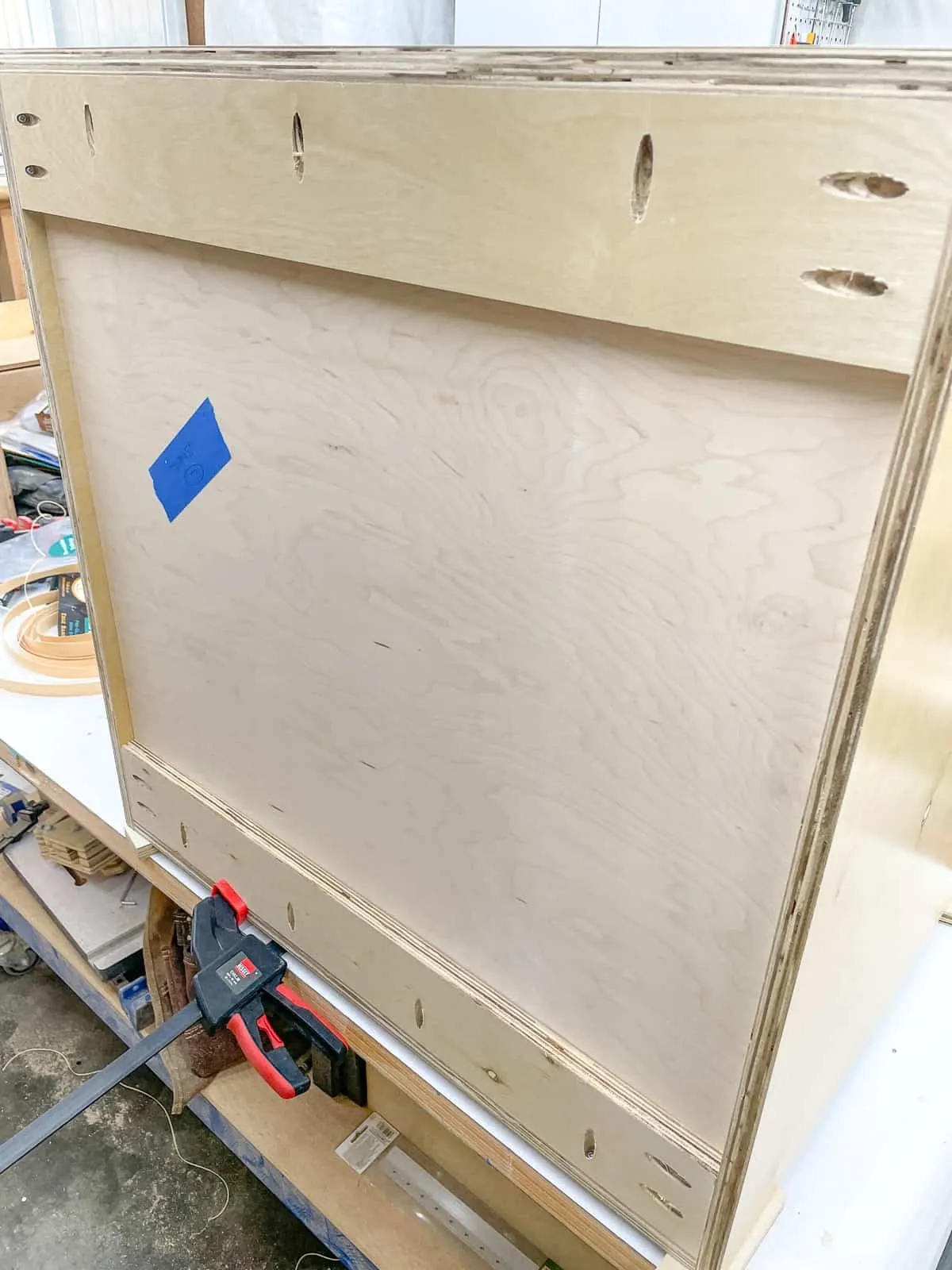
The groove is ¾" from the back of the cabinet, so the nailer strips can fit behind it. Use the nailer strip to set the table saw fence. ¾" plywood isn't exactly ¾", so this will give you a more accurate measurement.
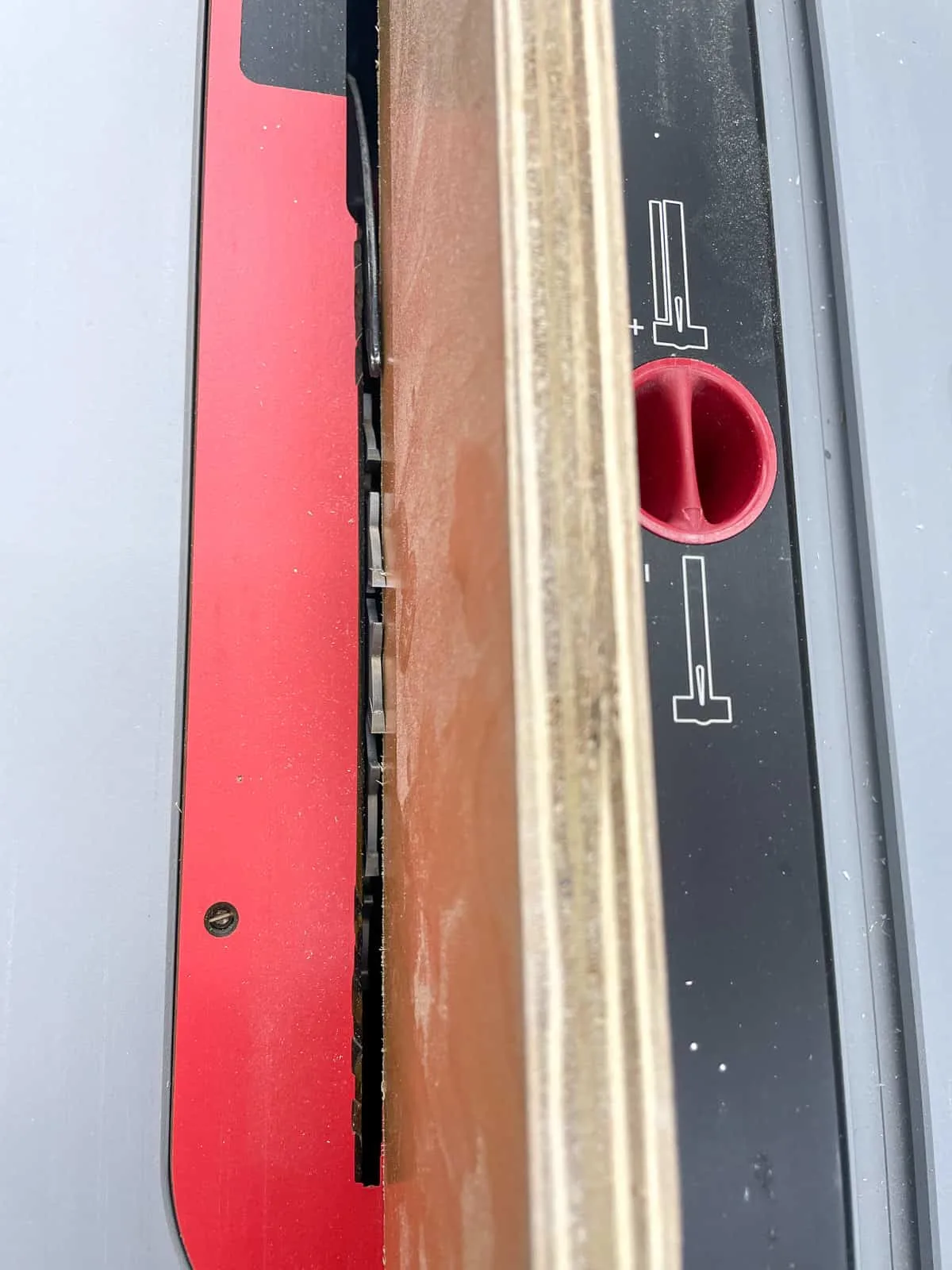
Set the table saw blade height to anywhere between ¼" and ⅜", so it cuts a third to halfway through the ¾" plywood. Make a test cut with the scrap piece of plywood. If everything looks good, set the test piece aside (you'll need it later!)
Cut the groove along the back edge of the side, bottom and back stretcher on the "good" face of each piece with this table saw setting.
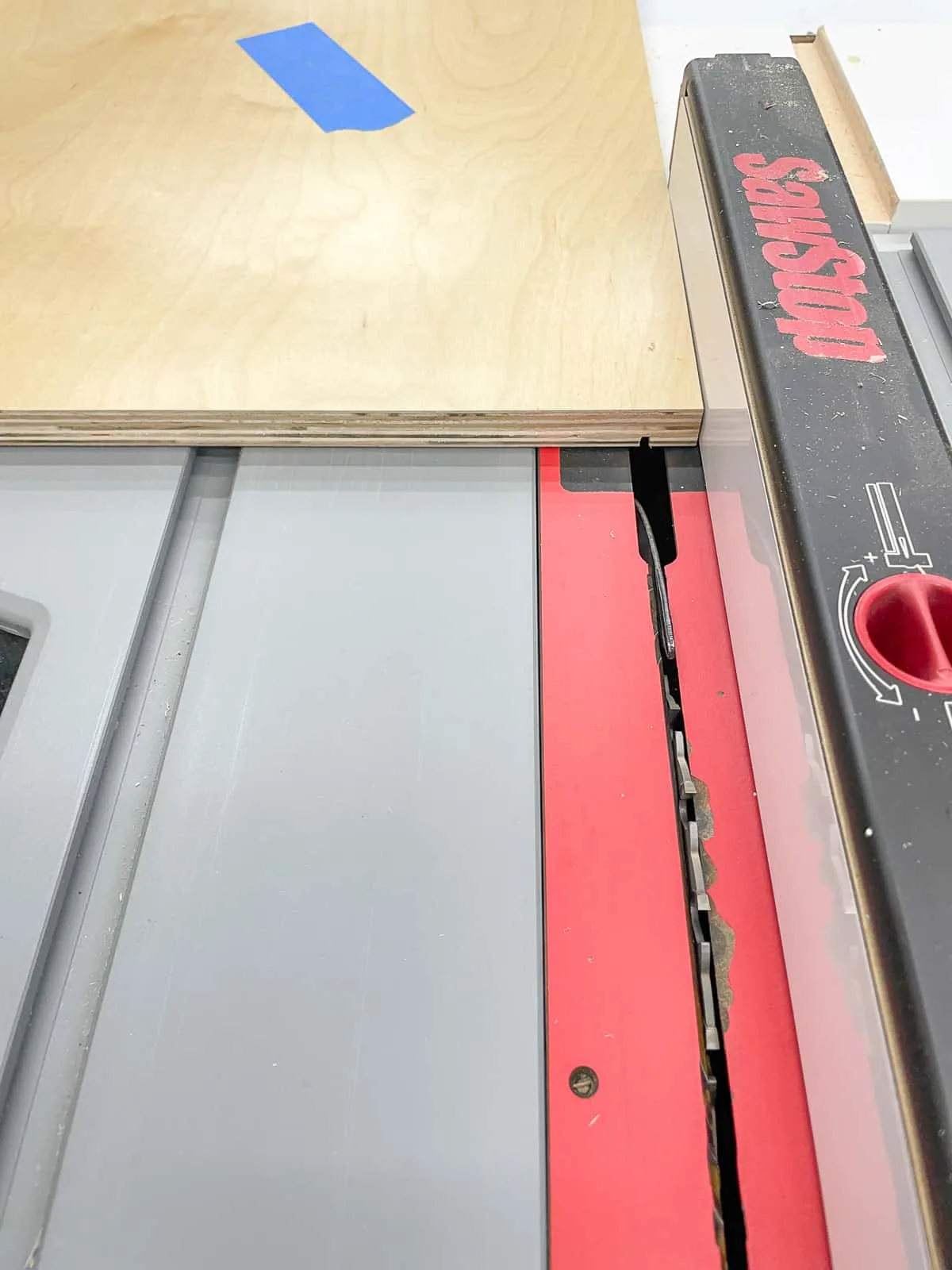
Now, grab your test piece again. Move your table saw fence slightly further away from the blade. I prefer to go about half a blade's width away to start with. Make a test cut to widen the groove.
Check the fit of the ¼" plywood in the groove. If it doesn't fit, move the fence over a tiny bit and cut it again. You want to get this fit tight enough to hold the back panel in place, but not so tight that it can't slide within the groove. It's better to make multiple cuts to sneak up on the fit, rather than cutting it too loose the first time.
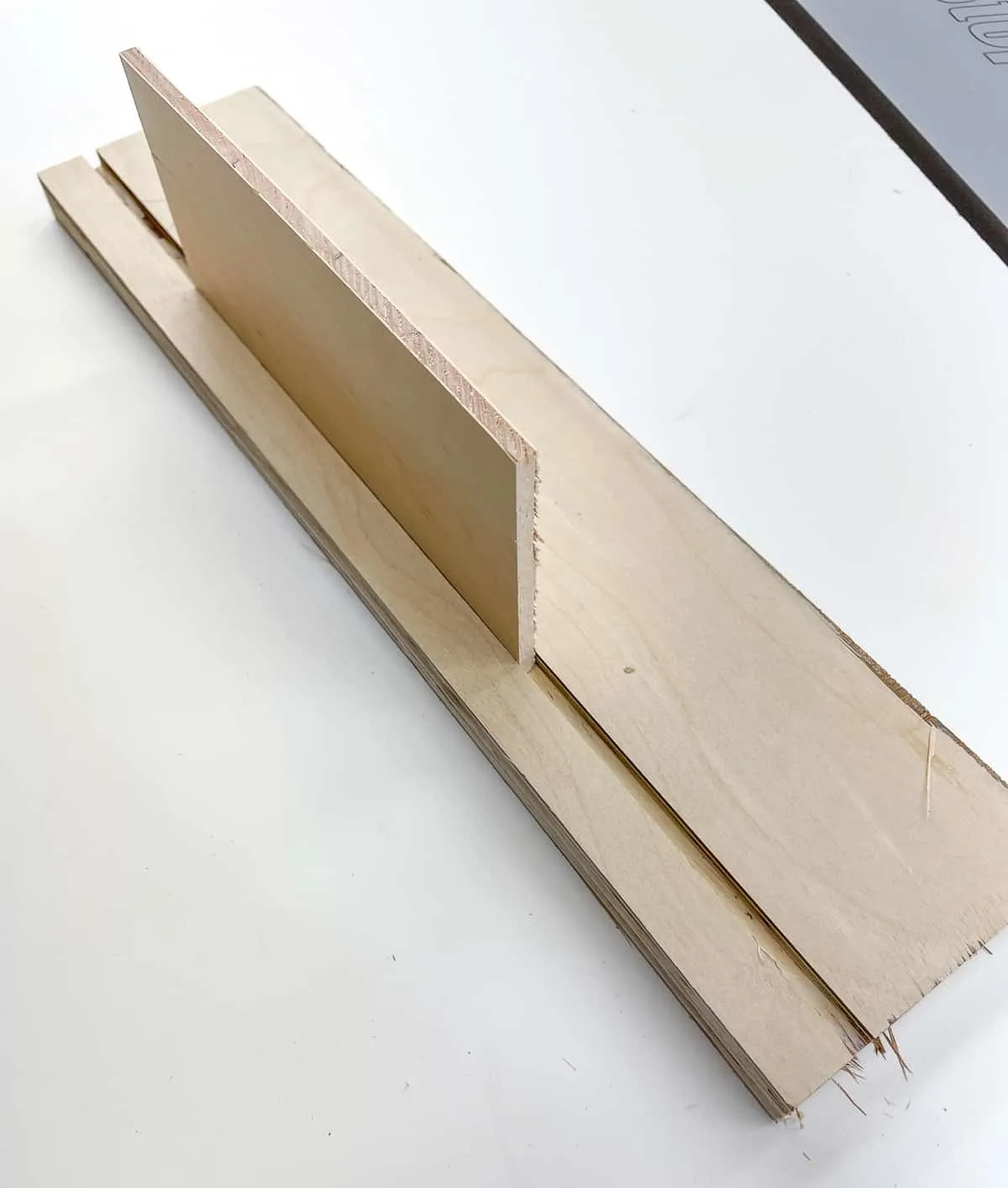
Once you have the fit dialed in, cut the wider grooves on the same sides, bottom and back stretcher pieces.
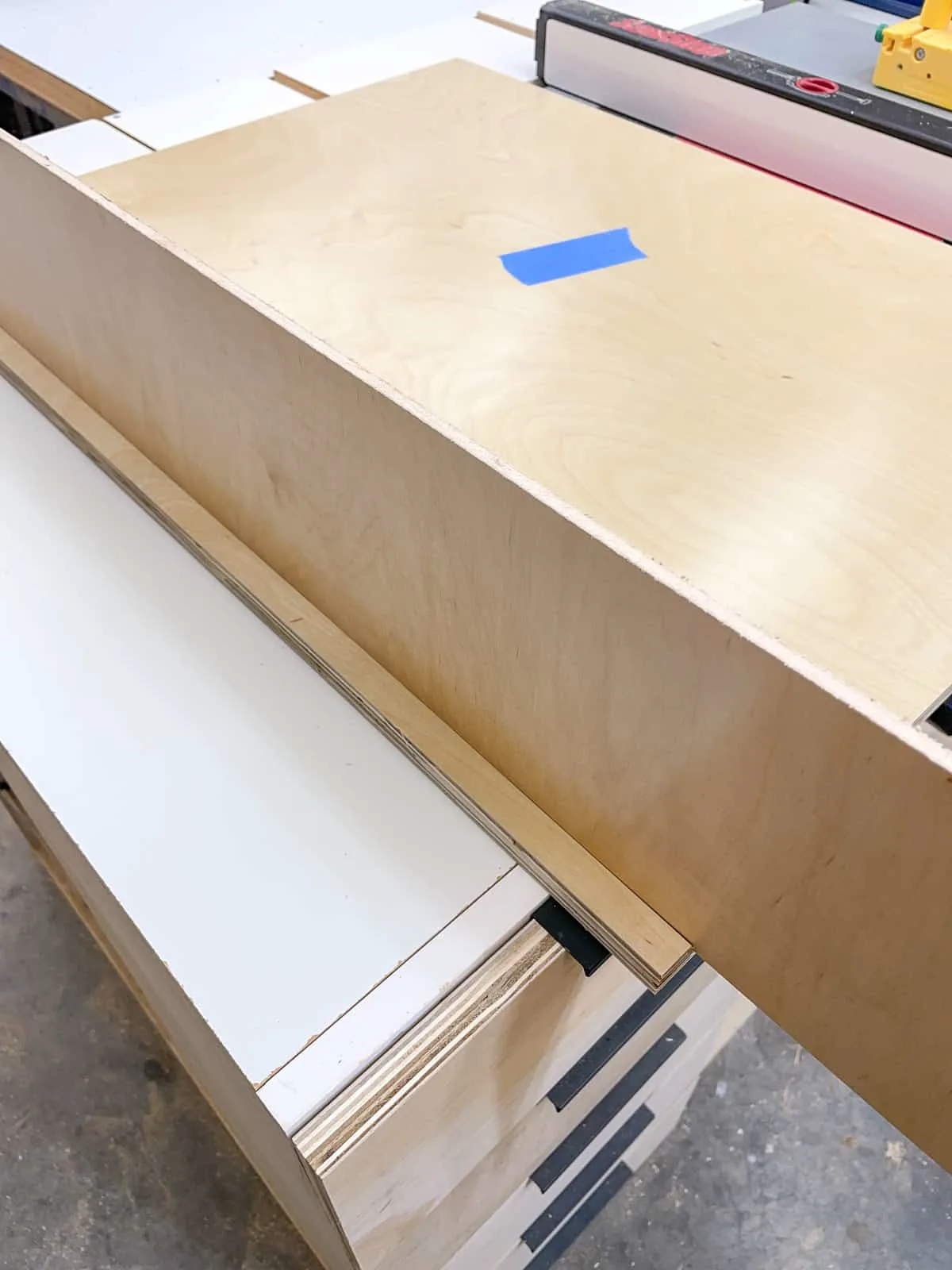
Apply edge banding to the front edges
If you're making frameless cabinets, you'll need to apply edge banding to all the front edges to hide the plywood layers. This includes the bottom, sides and front stretcher pieces.
Cut the edge banding to the length of your plywood piece and iron it on. I used prefinished birch edge banding to match the rest of the cabinet, so I don't have to paint or finish the edges. This special trimmer quickly cuts the sides flush with the plywood.
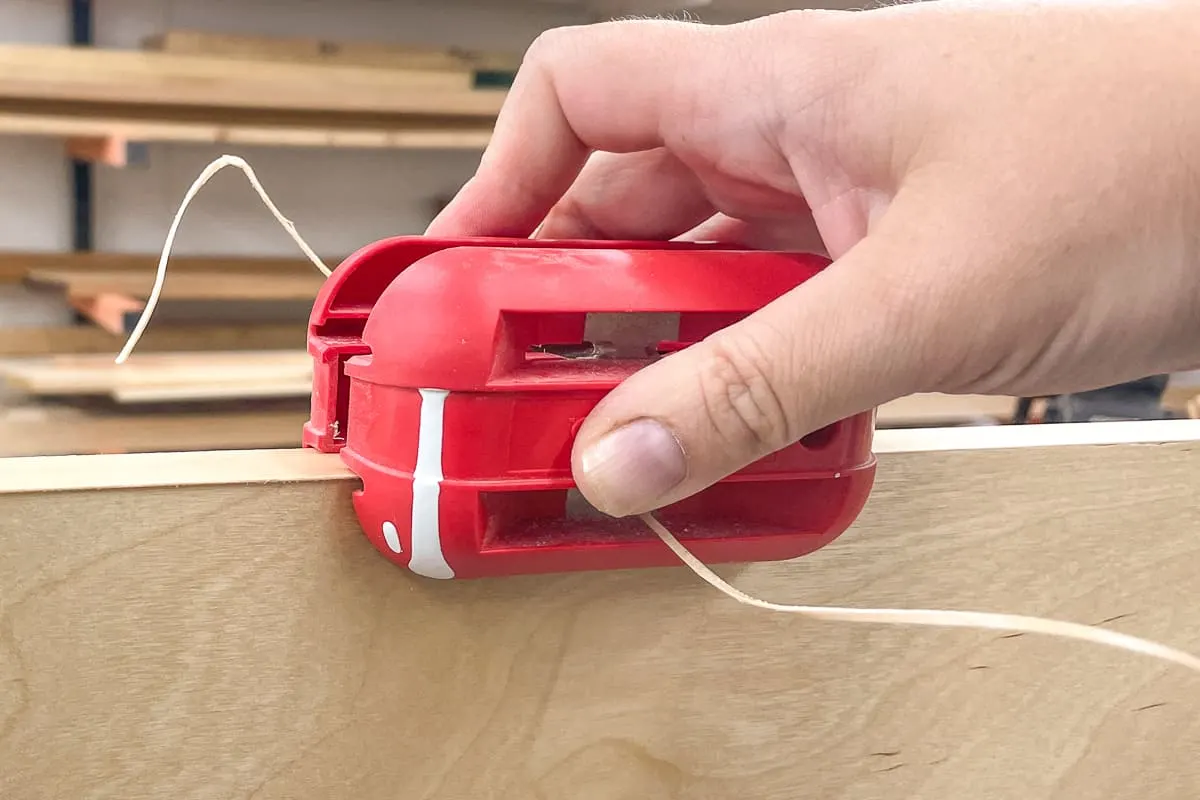
I have a full tutorial on how to apply edge banding if you want more information on this technique.
Drill pocket holes
The bottom, stretchers and nailer strips all require pocket holes along the ends. These pocket holes should be drilled in the opposite side from the groove, making sure you don't drill through it.
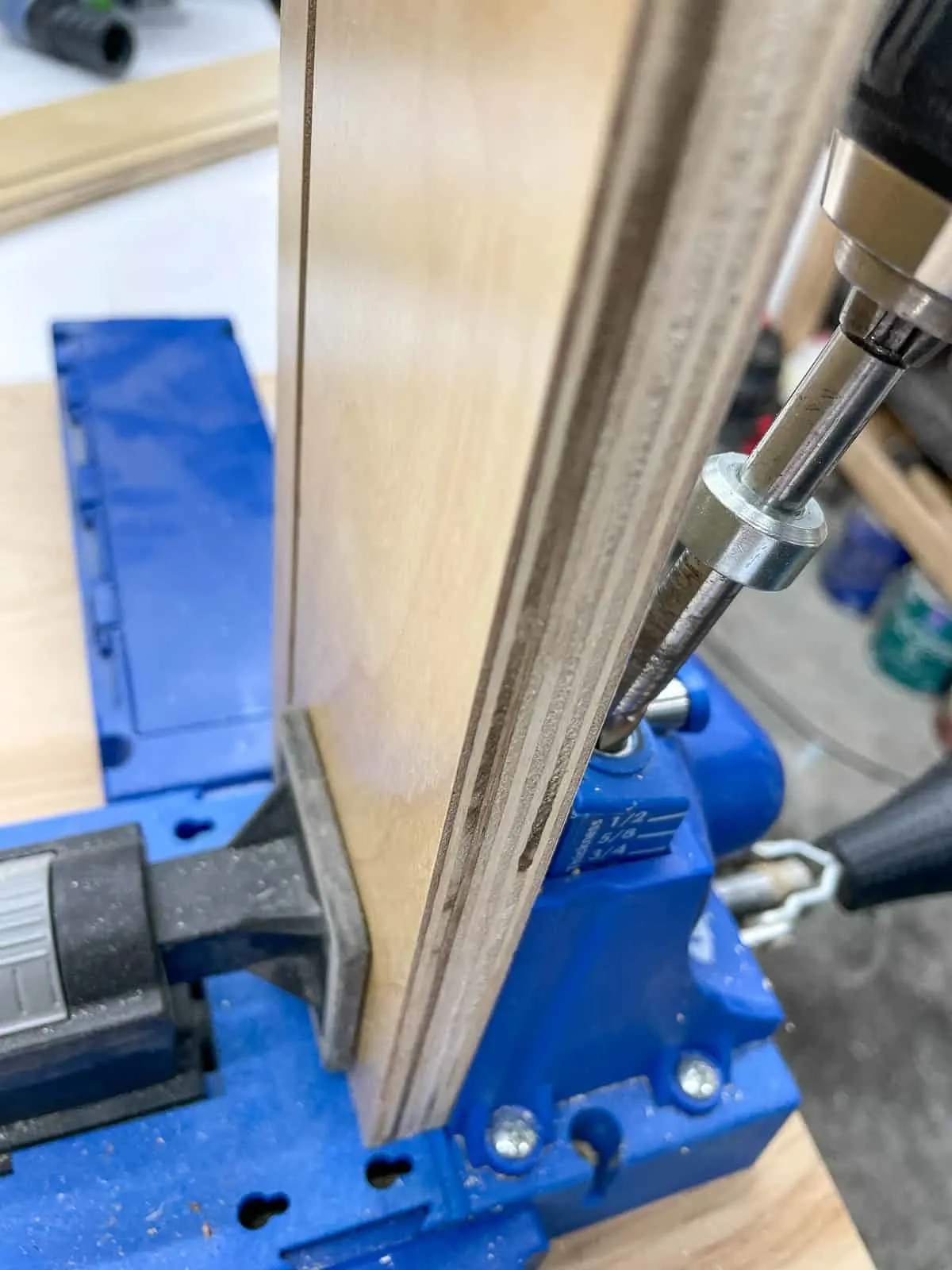
You can learn more about how to use a Kreg Jig here. Keep in mind that you should set the drill bit depth stop to slightly less then ¾" to account for the undersized plywood thickness.
Attach the bottom to the sides
Finally, it's time to start building this cabinet box! If everything was prepared correctly, this process should be really quick!
Start by attaching the bottom to the sides with 1 ¼" pocket hole screws. Make sure that all the edge banded sides are facing the same direction, and the grooves line up all the way around.
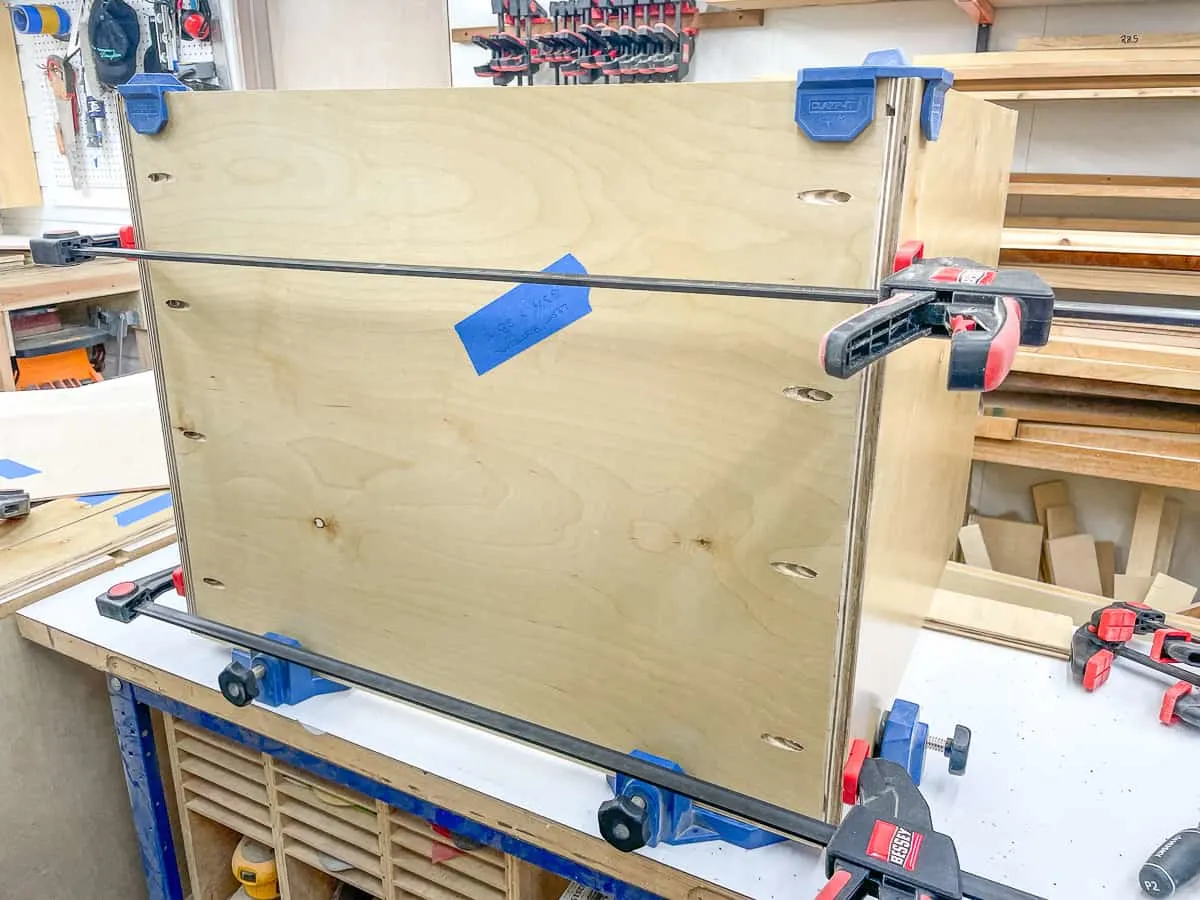
I highly recommend these Rockler corner clamps if you're assembling more than a few cabinet boxes. They act like another set of hands, holding those big plywood pieces together at a perfect right angle. I also use a couple long clamps in the middle so the edges don't shift as I'm driving in the screws.
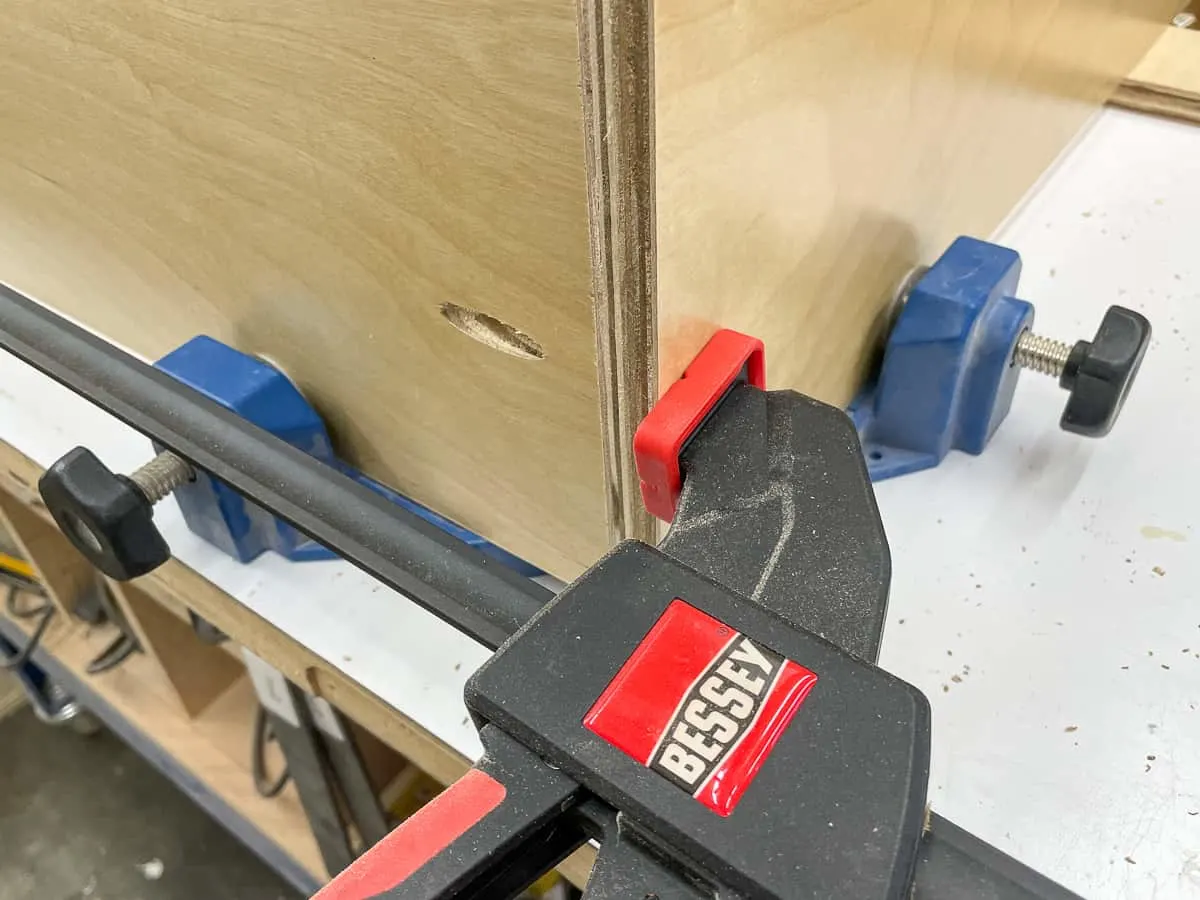
Attach the front stretcher
The front stretcher is the piece with pocket holes on the ends, edge banding on the front, and no groove cut into it. It will square up the cabinet box and serve as the cabinet door or drawer stop along the top. It also gives you something to screw into when attaching the countertop to the cabinet box.
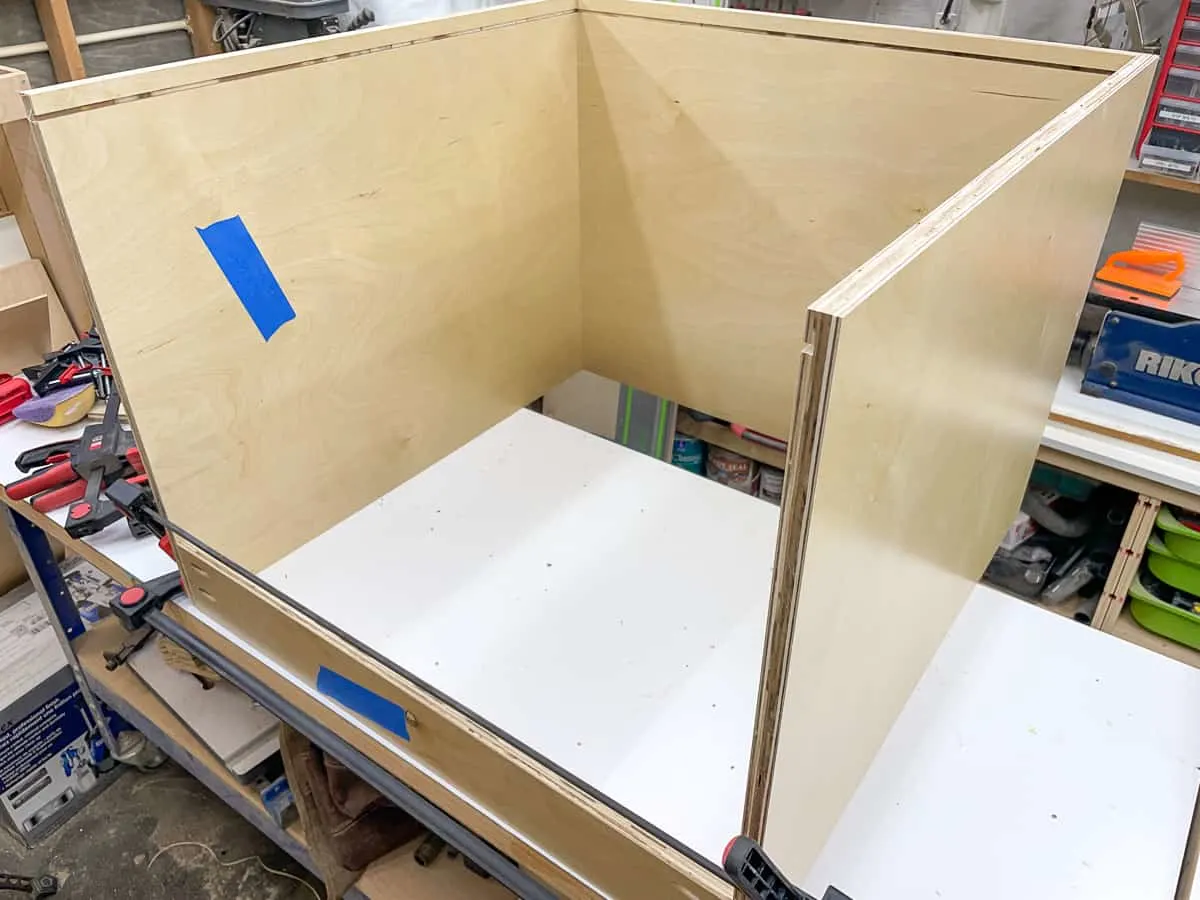
With the cabinet box facing down on the workbench, clamp the front stretcher between the two sides. Attach the front stretcher to the sides with 1 ¼" pocket hole screws.
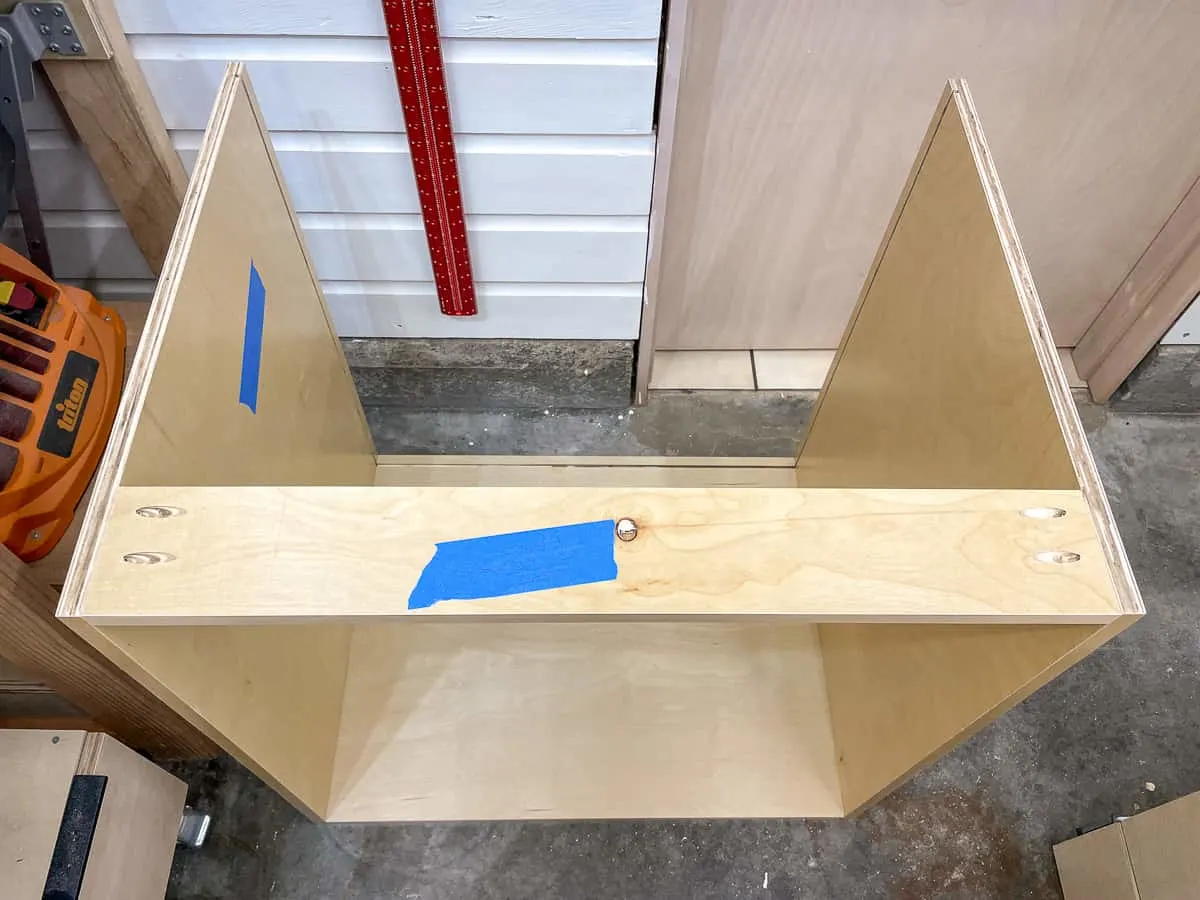
Insert the back panel
The ¼" cabinet back panel should slide smoothly into the grooves in the back. Remember that the "good" side of the plywood should face into the cabinet! Technically, the grain direction of the back panel should be vertical instead of horizontal, but this will be hidden behind drawer boxes so it doesn't really matter here.
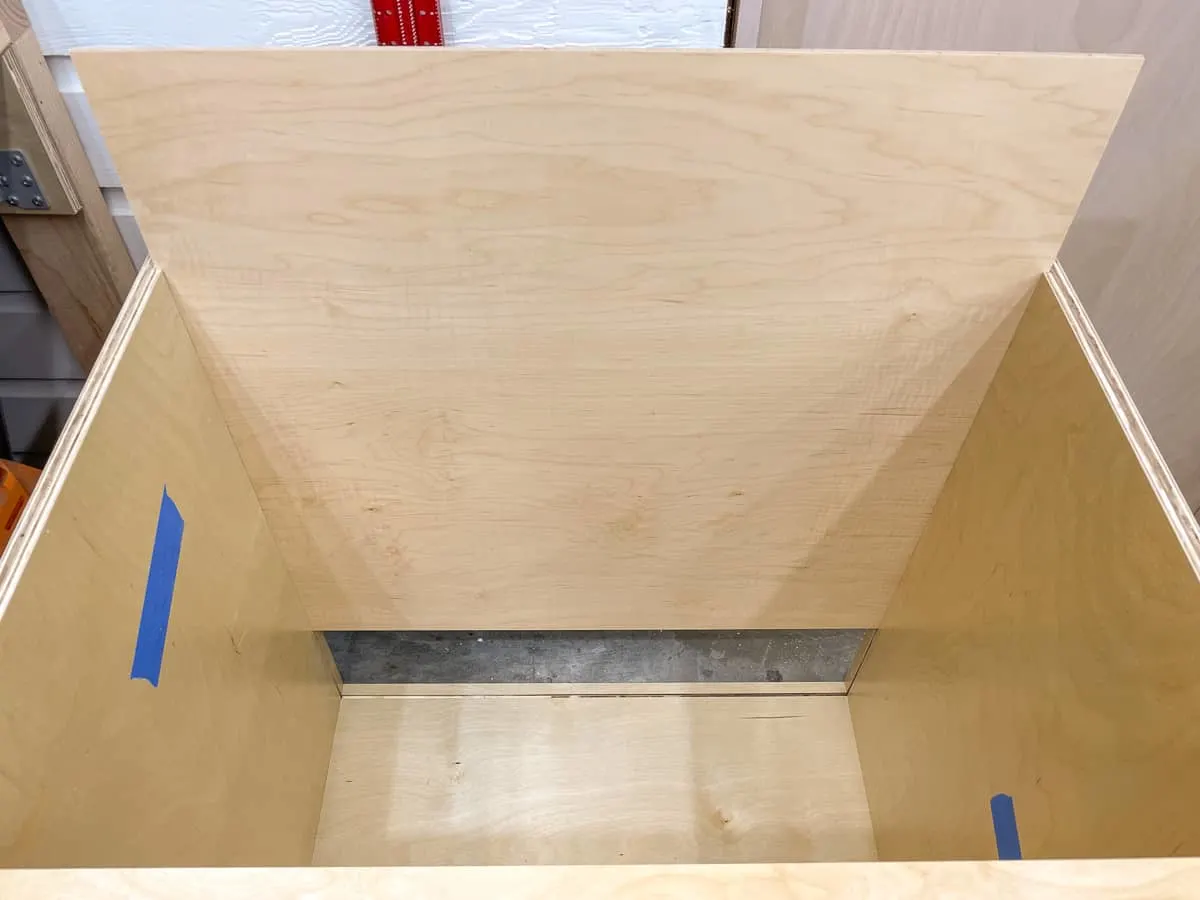
The back stretcher with the groove cut into it should fit right on top of the ¼" plywood, locking the panel into place.
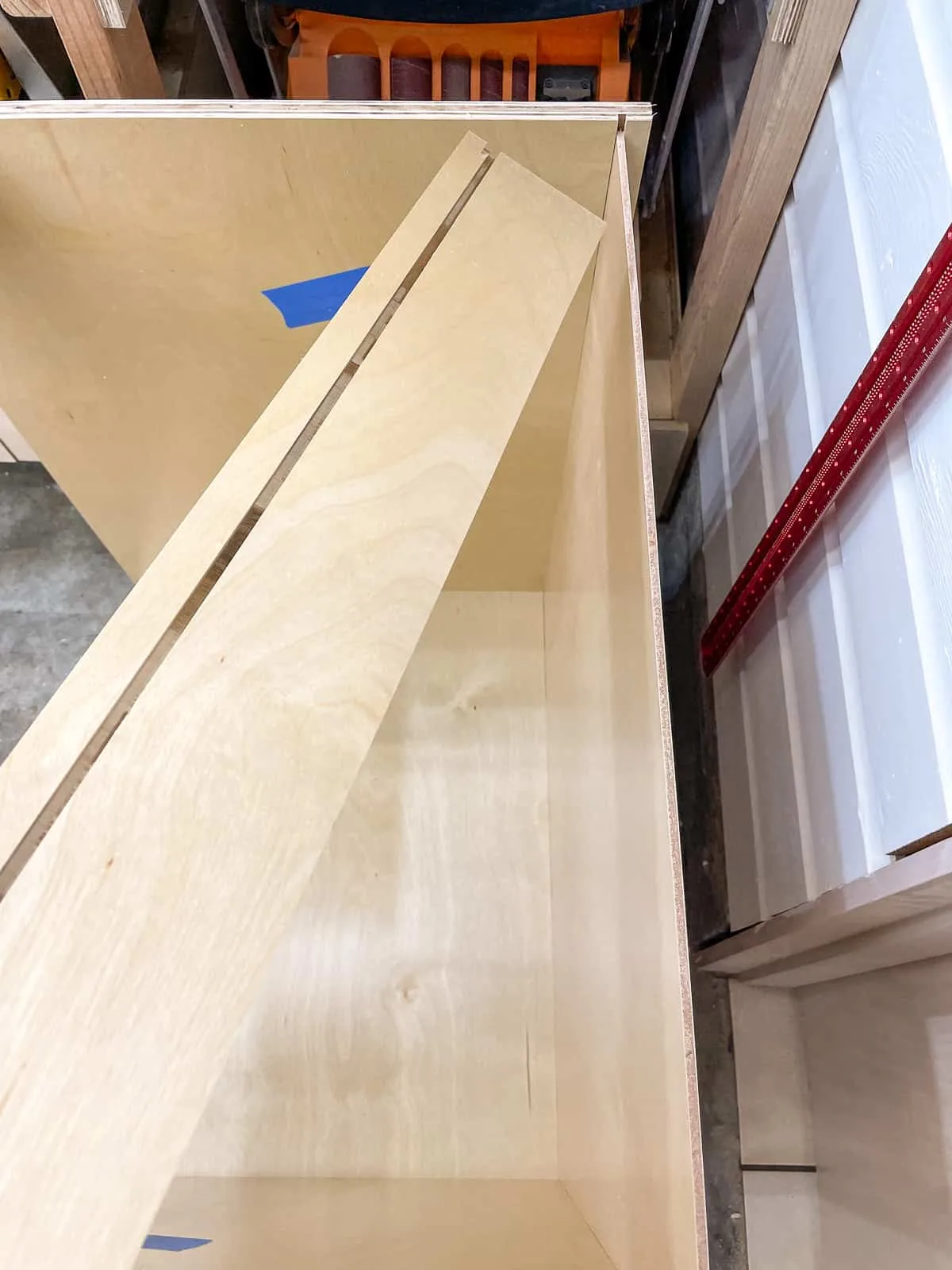
Use a clamp to hold the back stretcher flush with the top of the sides while you drive in the ¼" pocket hole screws.
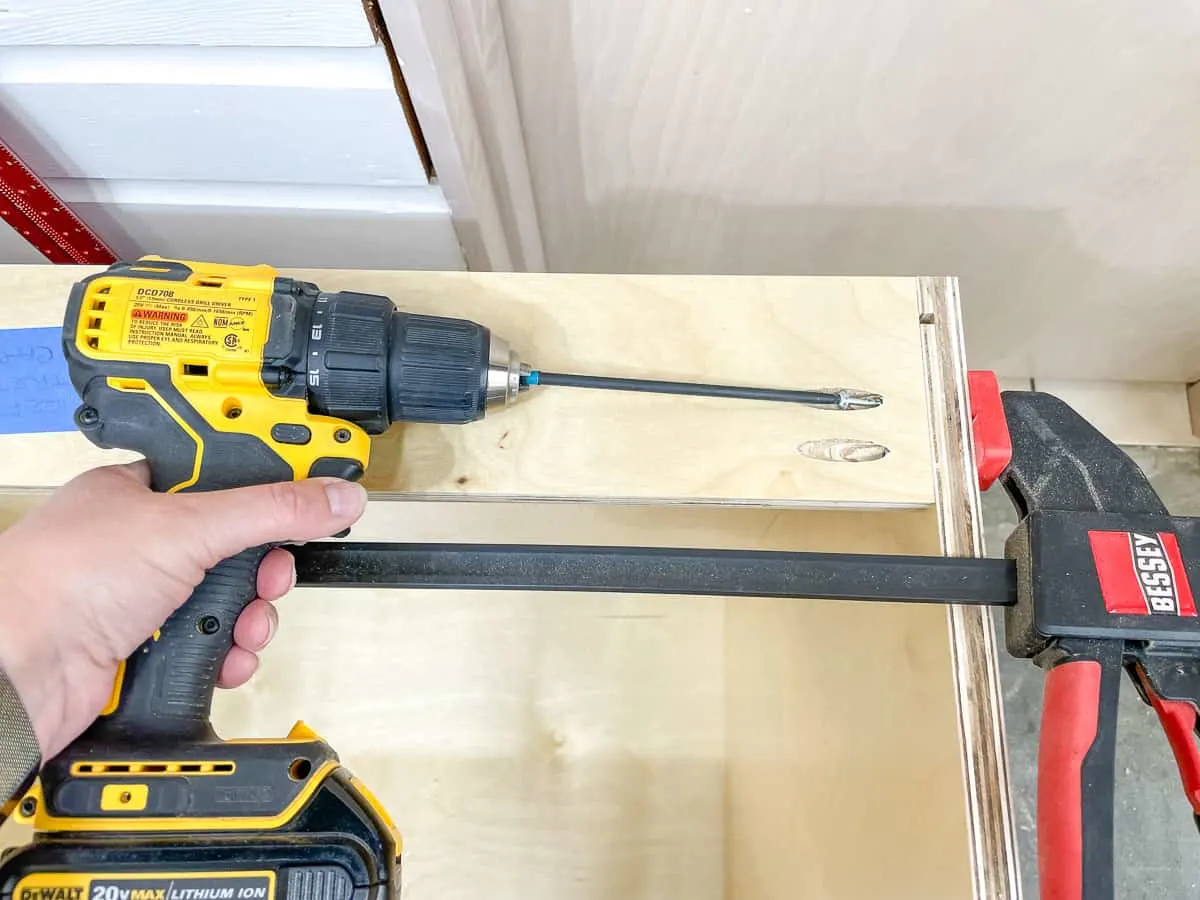
Attach the nailer strips
The nailer strips give you a solid board to screw through when attaching the cabinet box to the studs in the wall. Some people only attach a nailer strip to the top of the cabinet to save on materials. I like to have one at the top and the bottom, since we have less than straight walls and the cabinet box is usually only touching the wall in one of those spots.
Flip the cabinet onto its front, and place the first nailer strip under the back stretcher against the back panel. I drilled a few extra pocket holes along the top edge so that I could attach it to both the sides and the top.
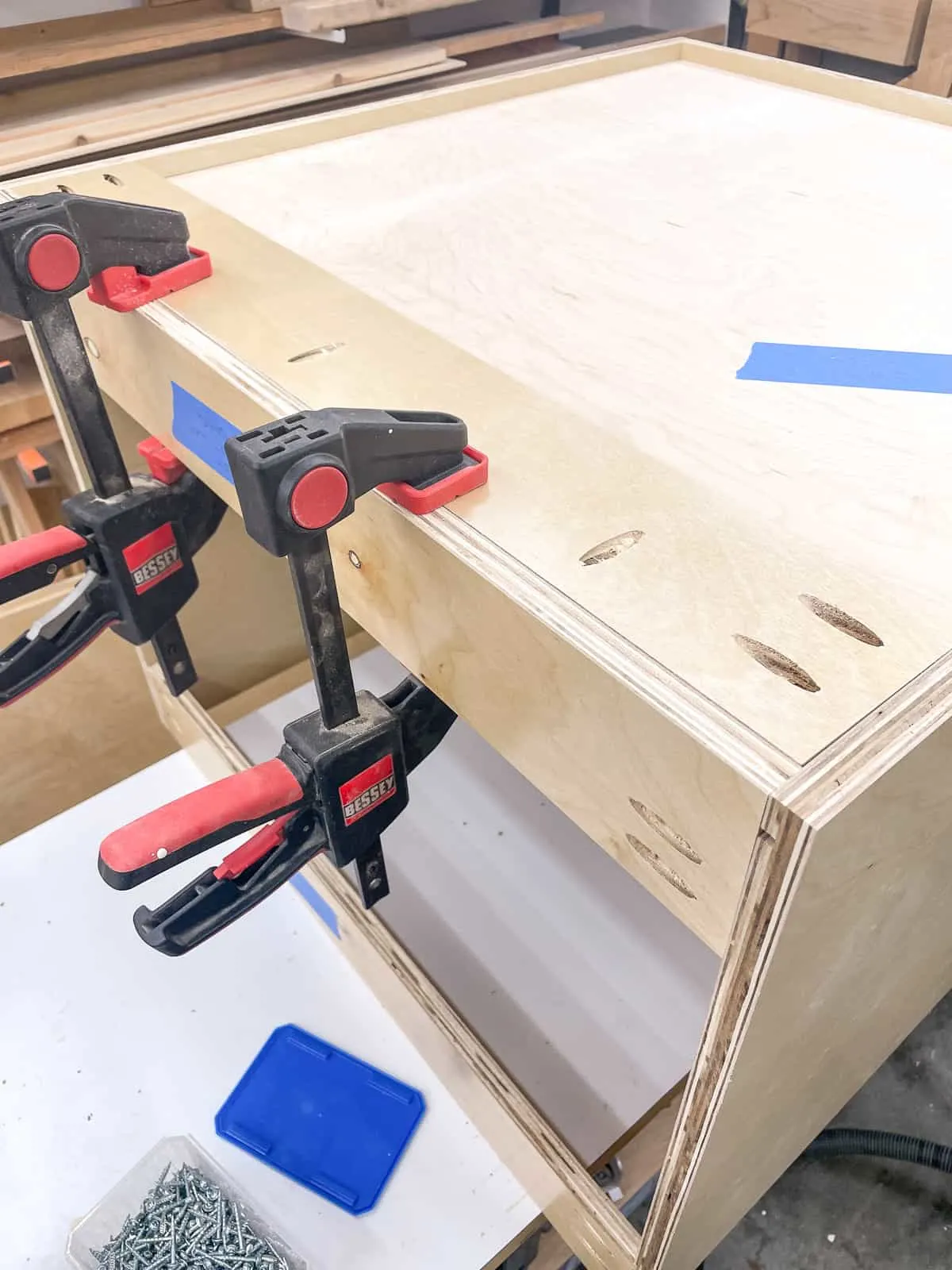
Repeat the process for the bottom nailer strip.
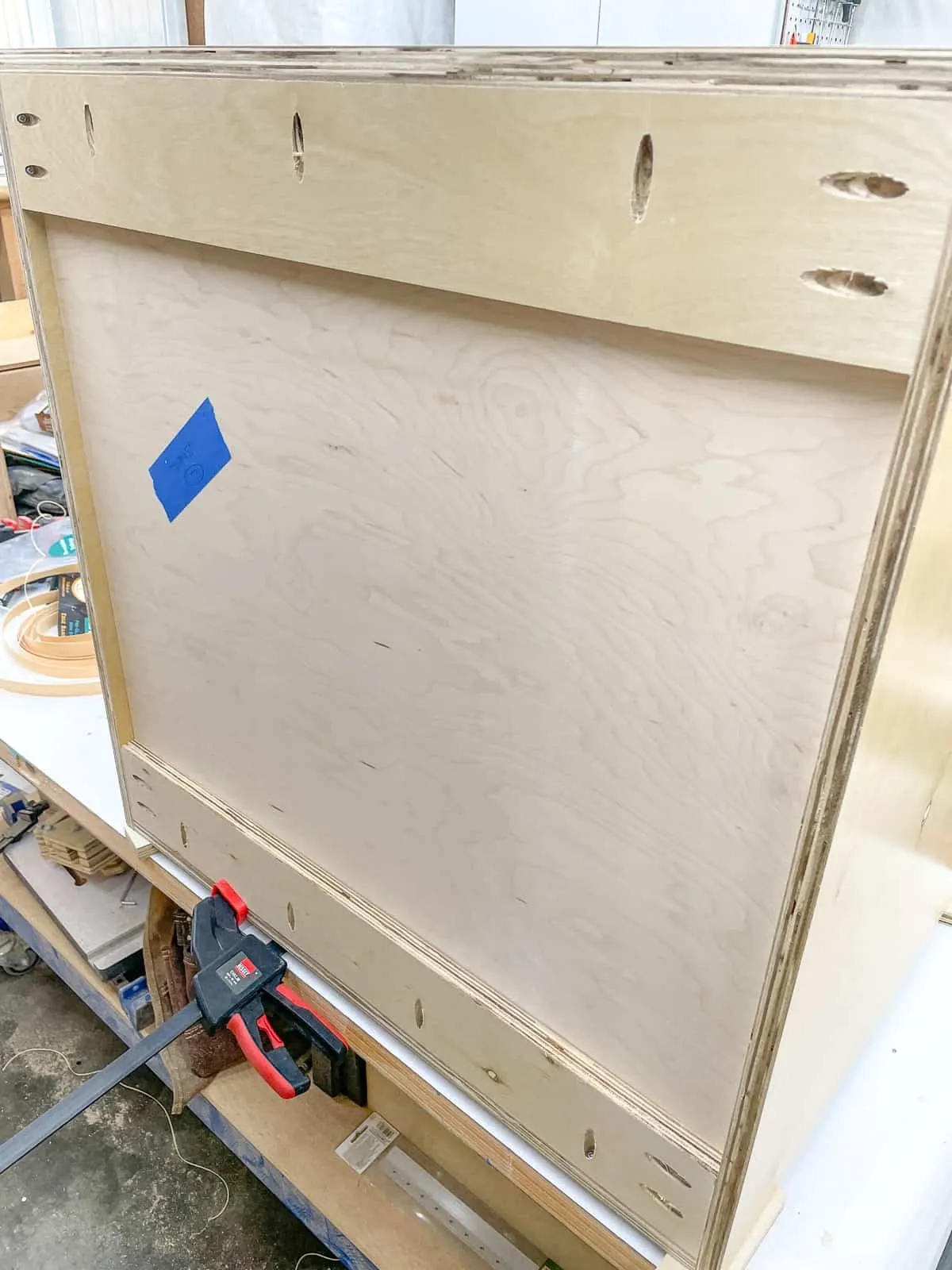
Add drawer supports (optional)
If you plan to install drawers, you'll need an additional piece underneath each one. This will support the undermount drawer slides I plan to use, and it also serves as a stop for the lower cabinet doors.
The drawer support is made the same way as the front stretcher. Cut it to fit inside the cabinet, with edge banding across the front and pocket holes on both ends.
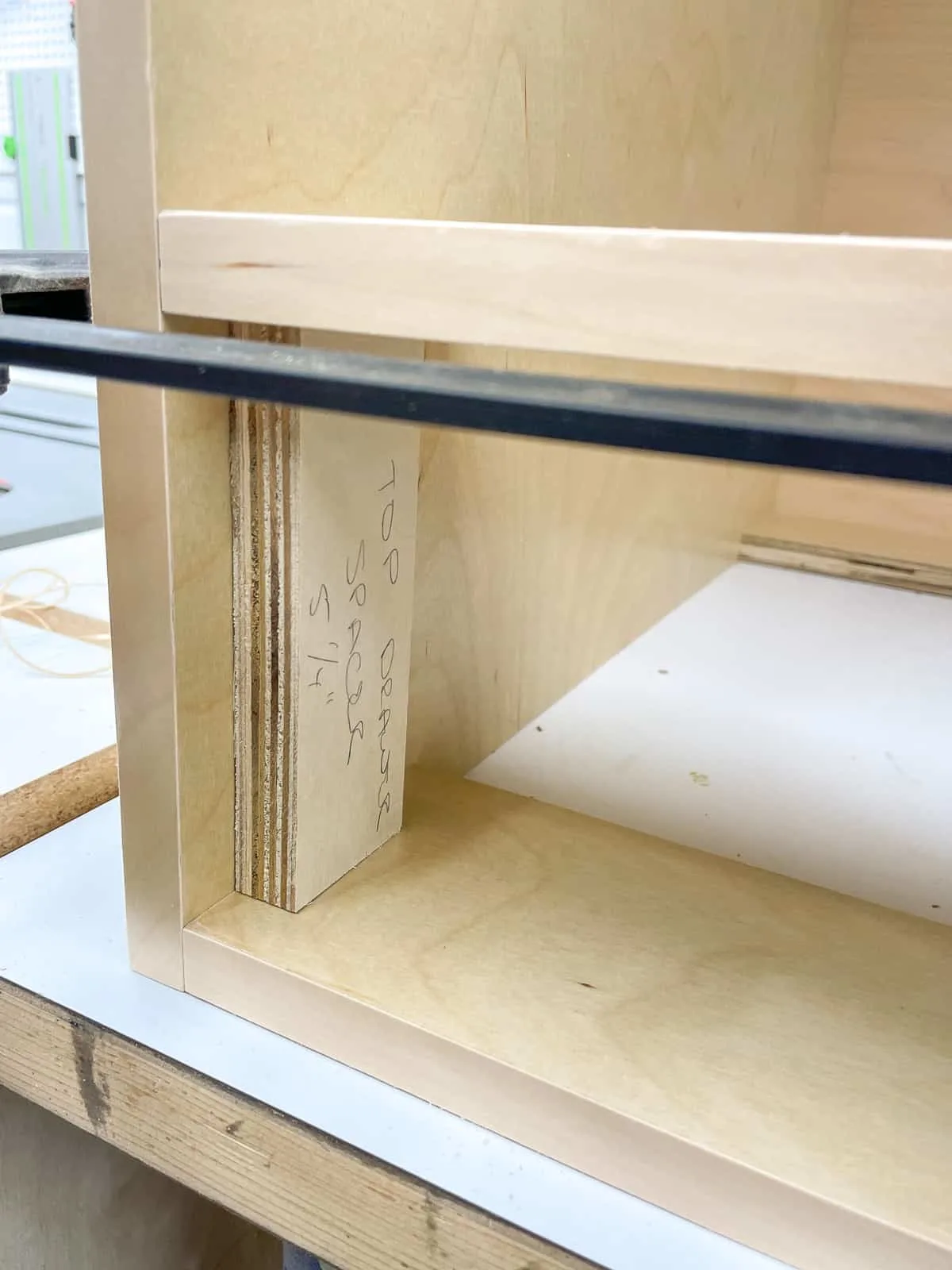
To ensure equal spacing across all your cabinet boxes, cut some spacers to the size of the drawer space. I always clearly label these so they don't accidentally end up in the trash! Flip the cabinet onto its top, and place the spacers on top of the front stretcher. Then place the drawer support on top, clamp it into place and secure it with pocket hole screws.
Congratulations, you just finished building a basic cabinet box!
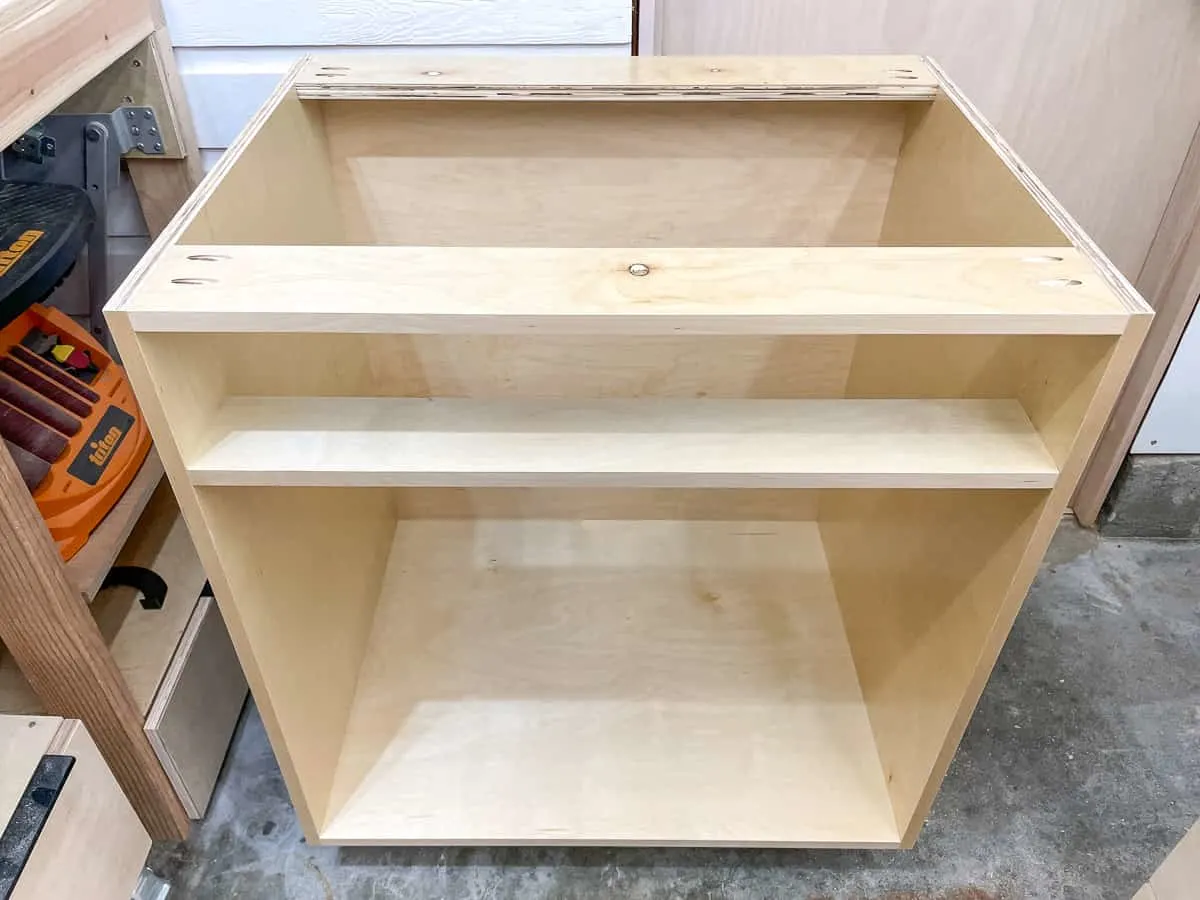
Assemble the toe kick platform
The toe kick can be made from 2x4s or any ¾" material. It'll be hidden behind the toe kick molding after it's installed, so it doesn't matter what it looks like. Just make sure to stick to one height across all the platforms!
The width of the toe kick platform should match the width of the cabinet. The depth can vary depending on how deep you want your recess to be. Anywhere between 3" and 4" tall and deep is standard.
When I tore out my old kitchen cabinets, I discovered that some of them were installed before the tile, leaving a sunken area. I filled it in with ¼" cement board, but it still isn't quite flush. I made the toe kick recess 3" deep so that it could sit on the tile instead of the uneven surface behind. Yet another reason why I prefer the separate toe kick!
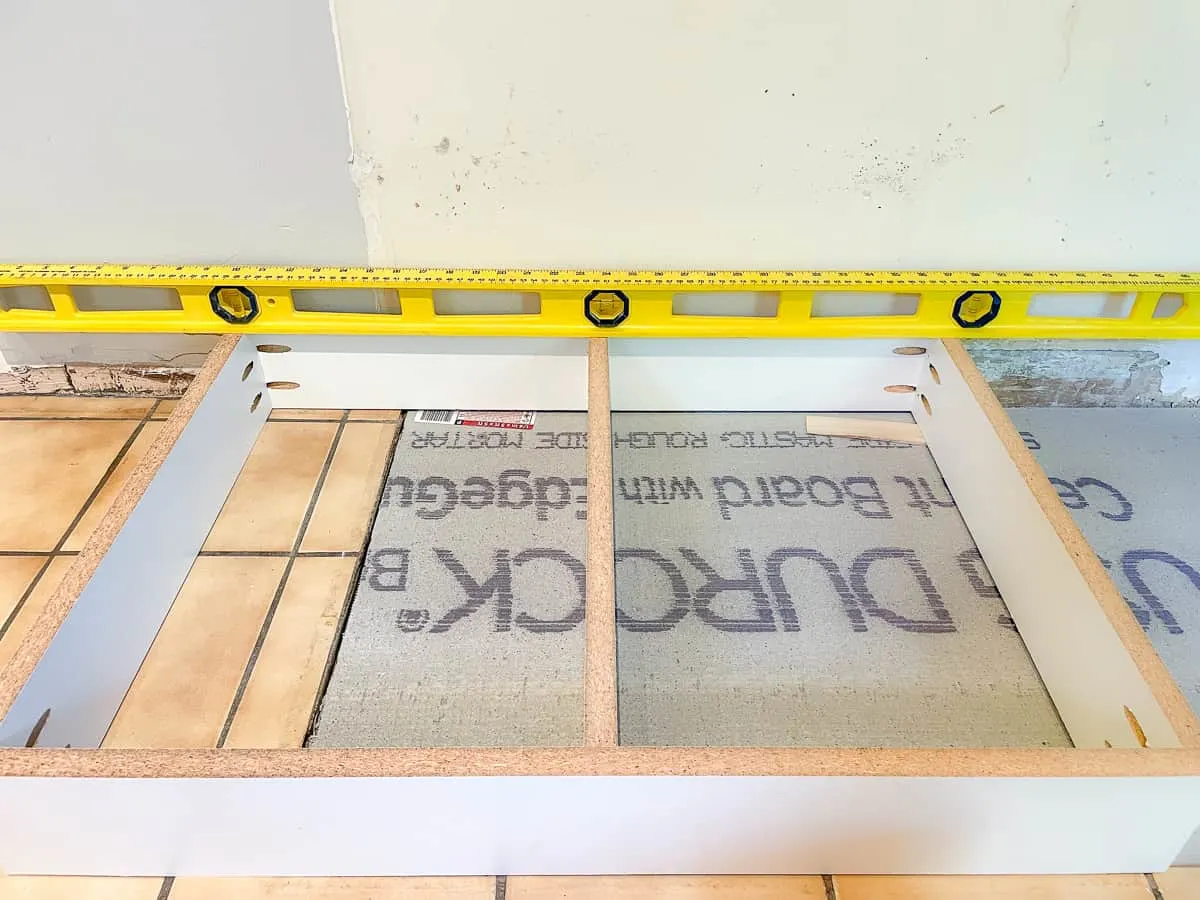
The cabinet box sits on top of the platform, and both the platform and the cabinet are secured to the wall at the studs. I'll go into more detail about how to level and install the toe kick platform and the cabinet here. It's not as difficult as you might think!
Now that you know how to build a simple cabinet box, you can build an entire kitchen! If you batch out each step, you can put together multiple cabinets in a weekend. Next, I'll show you how to build a drawer to go inside your new base cabinets!
Check out these other kitchen remodel projects!